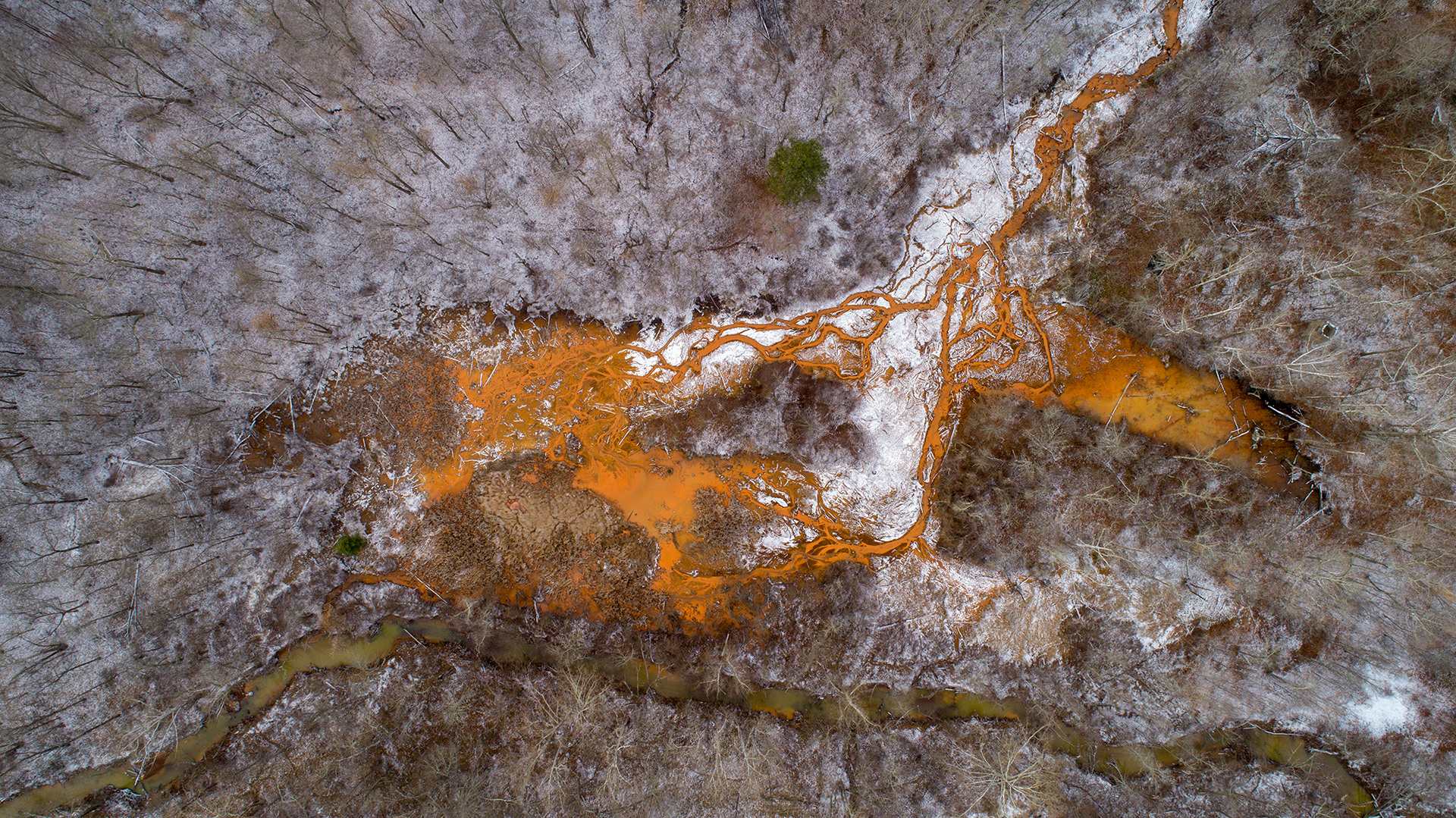
From Pollution to Paint
How an engineer, an artist, and the community are working together to turn acid mine drainage into a paint pigment product
Story by Andrea Gibson
Photos and Video by Ben Siegel
Civil engineer Guy Riefler and artist John Sabraw pulled the iron-rich sludge from polluted streams in southeastern Ohio and transformed it into a paint pigment. This engineering feat—and its implications for the environment, the local economy, and art—has attracted attention from government and nonprofit groups, the art supply industry, scientists and engineers, as well as global media outlets such as Al Jazeera and the Weather Channel.
After almost a decade of laboratory research to perfect the process, the Ohio University faculty members, in conjunction with nonprofit organization Rural Action, launched a pilot production facility in Corning, Ohio, in summer 2018. With funding from the Sugar Bush Foundation and a donation from OHIO alumnus Dick Dickerson, the team designed and built a system to capture the iron runoff from an old coal mine and use it as the basis for professional artist-grade paint pigment. The runoff—a common problem in the region known as acid mine drainage—has been polluting the mainstem of Sunday Creek that runs through the village of Corning for decades. If the pilot project is a success, it would not only generate the raw materials for a marketable product, but a larger scale version of the facility also could clean the pollution from the stream, opening up new recreation and tourism possibilities for the former coal community.
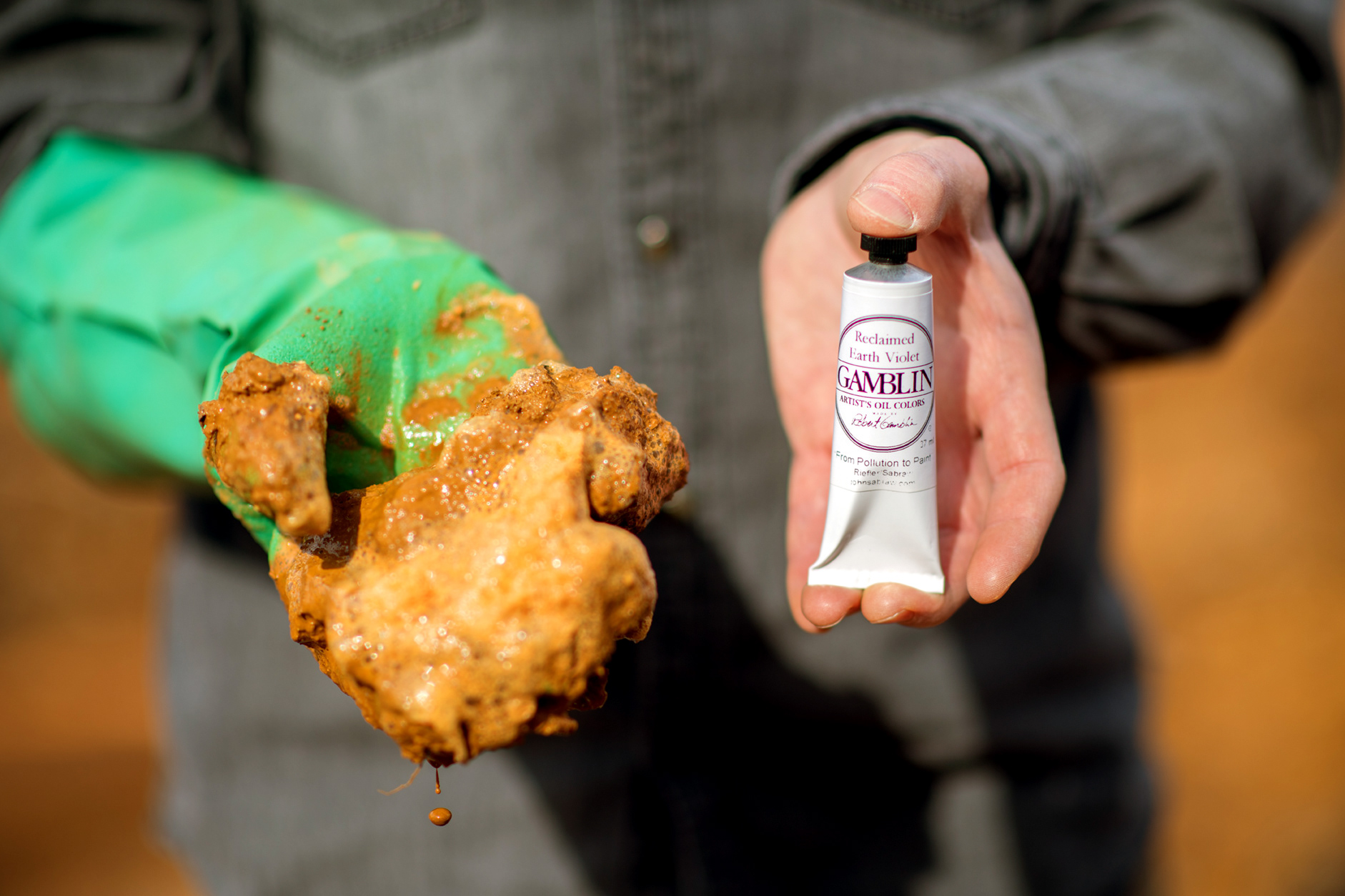
“If we can convert this into a commodity, we can change this from a problem to something we can enrich the community with,” says Riefler, a professor and chair of civil engineering in the Russ College of Engineering and Technology.
The team plans to operate the pilot plant 24 hours per day through late fall, constantly monitoring and troubleshooting processes—previously tested in a lab setting—to meet the goal of producing a pound of iron oxide per day, Riefler says. The iron must be pure enough to produce an attractive paint pigment that industry will purchase, he notes.
A full-scale facility—which would be required to produce enough iron oxide to meet the demands of the art supply industry and clean up the stream—would cost about $4.5 million. Although that figure sounds like a lot, “if you look at the dollar per stream mile, this looks like a good buy,” as such a facility could restore miles of a long-troubled branch of Sunday Creek, says Michelle Shively, an Ohio University alumna who serves as the Sunday Creek Watershed Coordinator for Rural Action, an Athens County-based non-profit organization.
While the acid mine drainage remediation project addresses a very local problem, it’s been eye-opening to see how much it also has sparked a conversation with people around the world—from the news media and general public—about some broader questions about how scientists, artists, students, and community members can join forces to tackle big issues, says Sabraw, professor and chair of painting and drawing in the School of Art + Design in the College of Fine Arts.“The (project) has really given me a perspective on how pursuing a crazy idea at this level can have an impact on a broader scale,” Sabraw says. “I hadn’t expected that at all.”
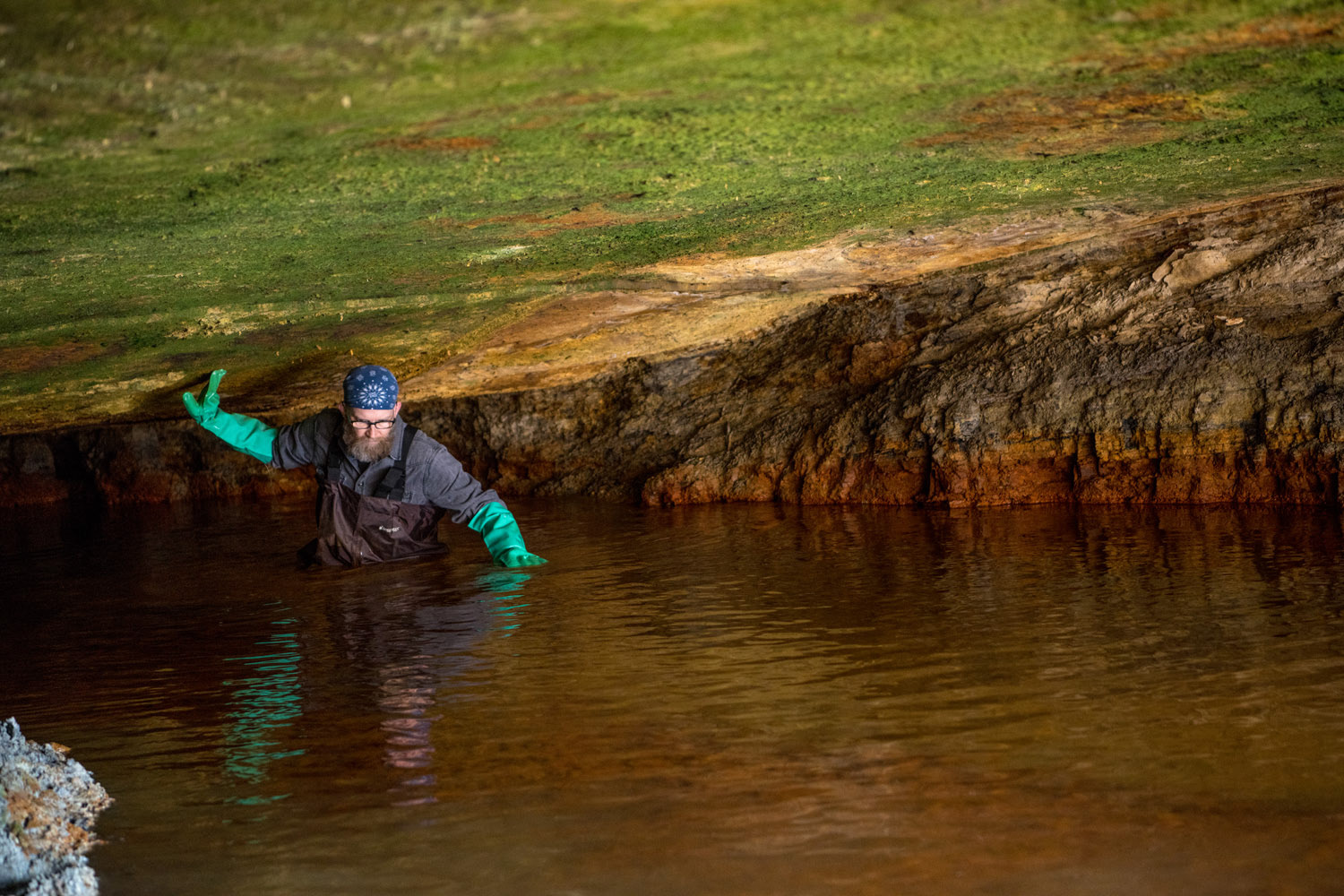
THE POLLUTION PROBLEM
Water seeping through the region’s many old coal mines washes heavy metals such as iron and aluminum into the local waterways, turning them a rust orange or milky white hue. At some affected streams, equipment has been installed to release alkaline lime to neutralize the acid mine drainage and make the water habitable for insects, fish, and other wildlife. One tributary of Sunday Creek has seen 17 species of native fish return after treatment began, and Monday Creek now boasts 37, up from 4 species when we began, according to Shively. “We’ve brought life back to miles and miles of streams,” she says.
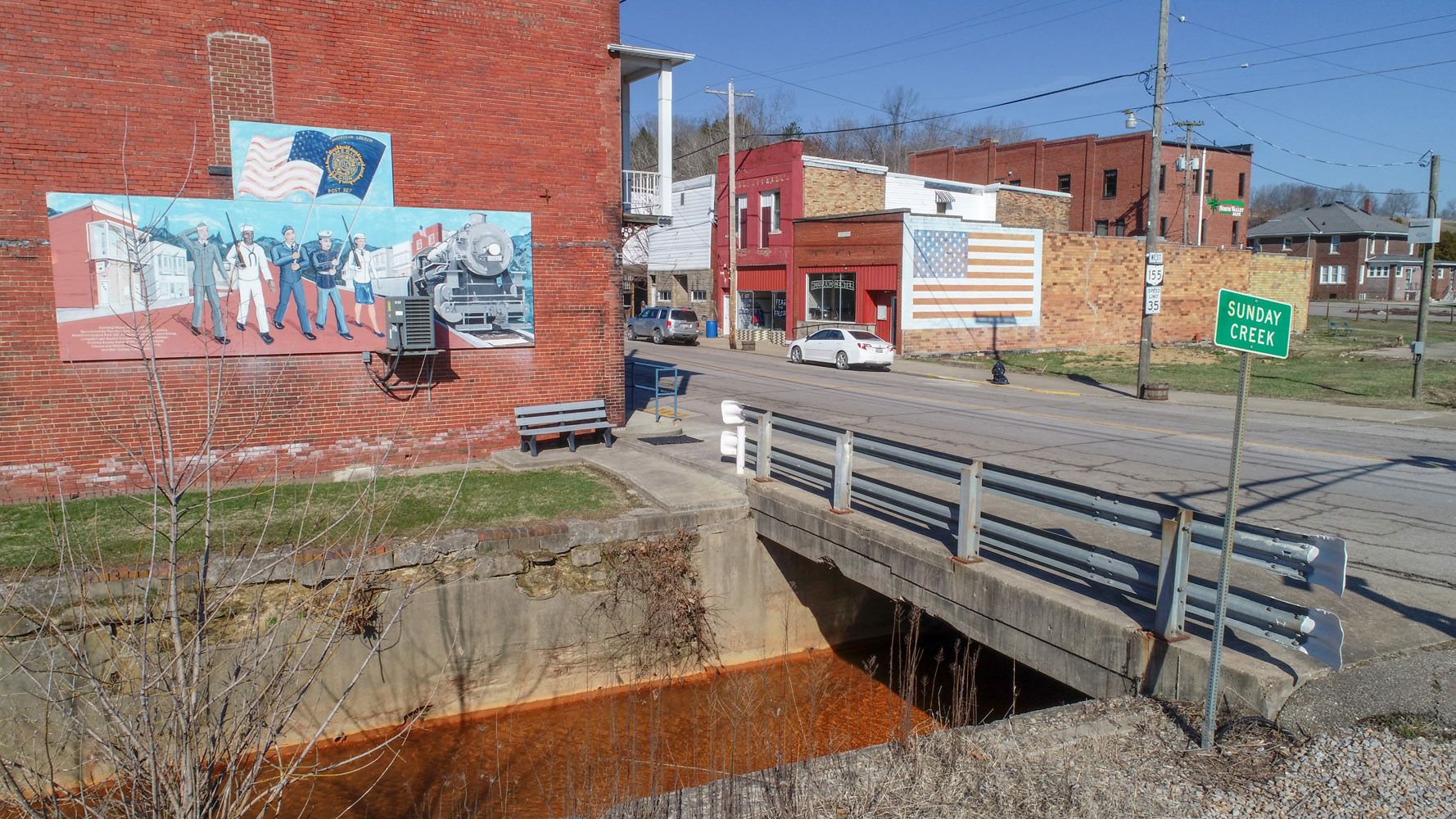
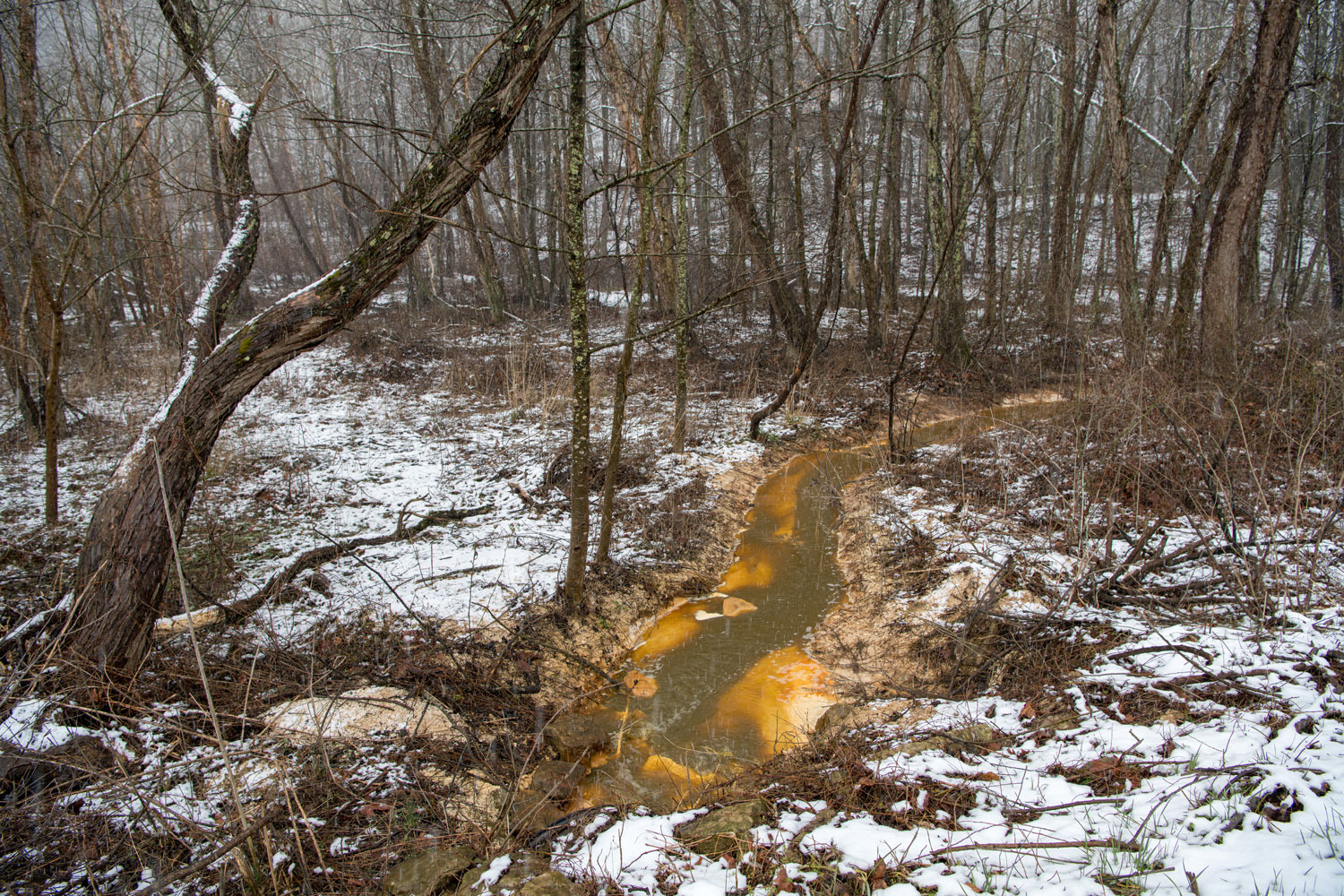
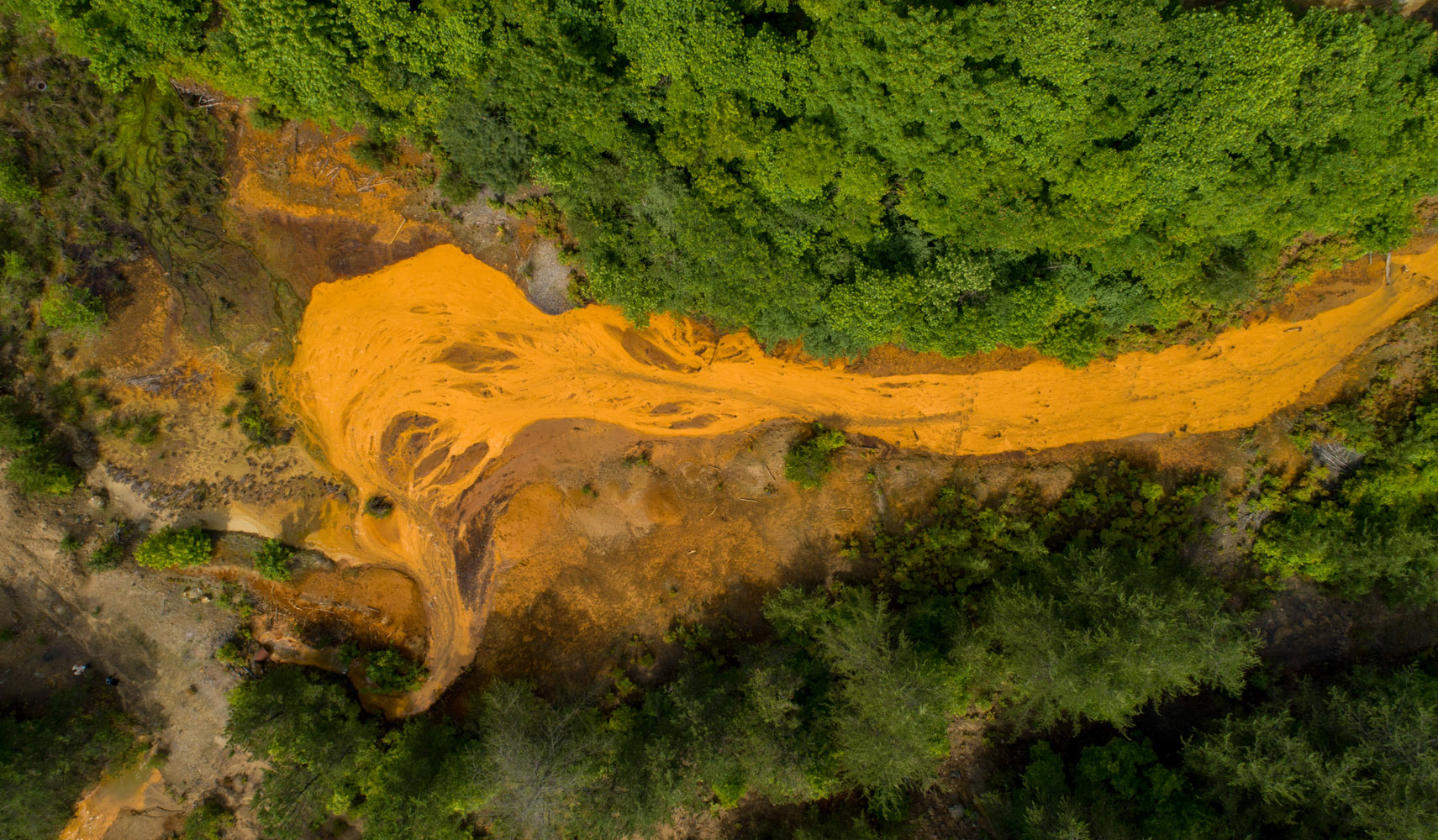
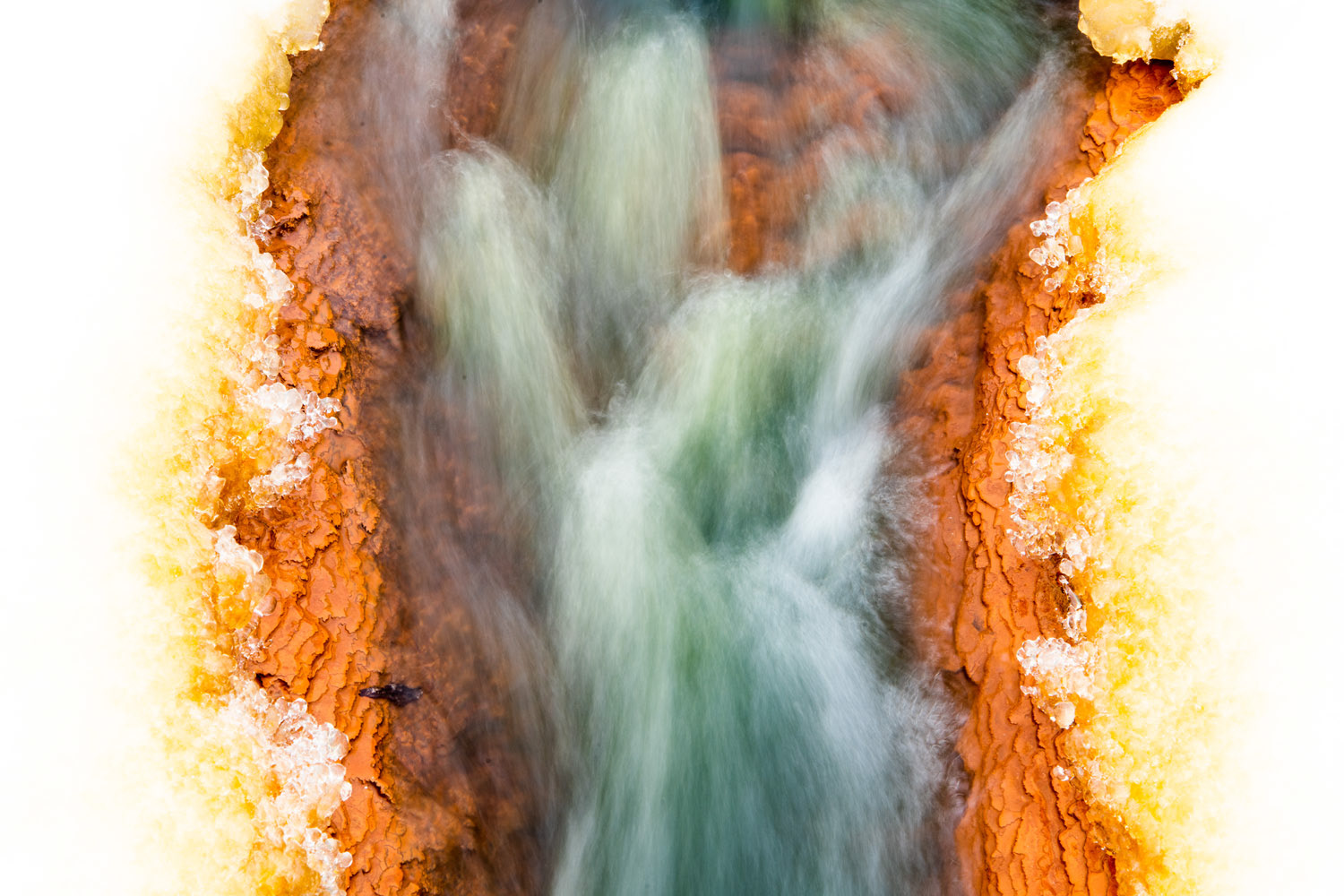
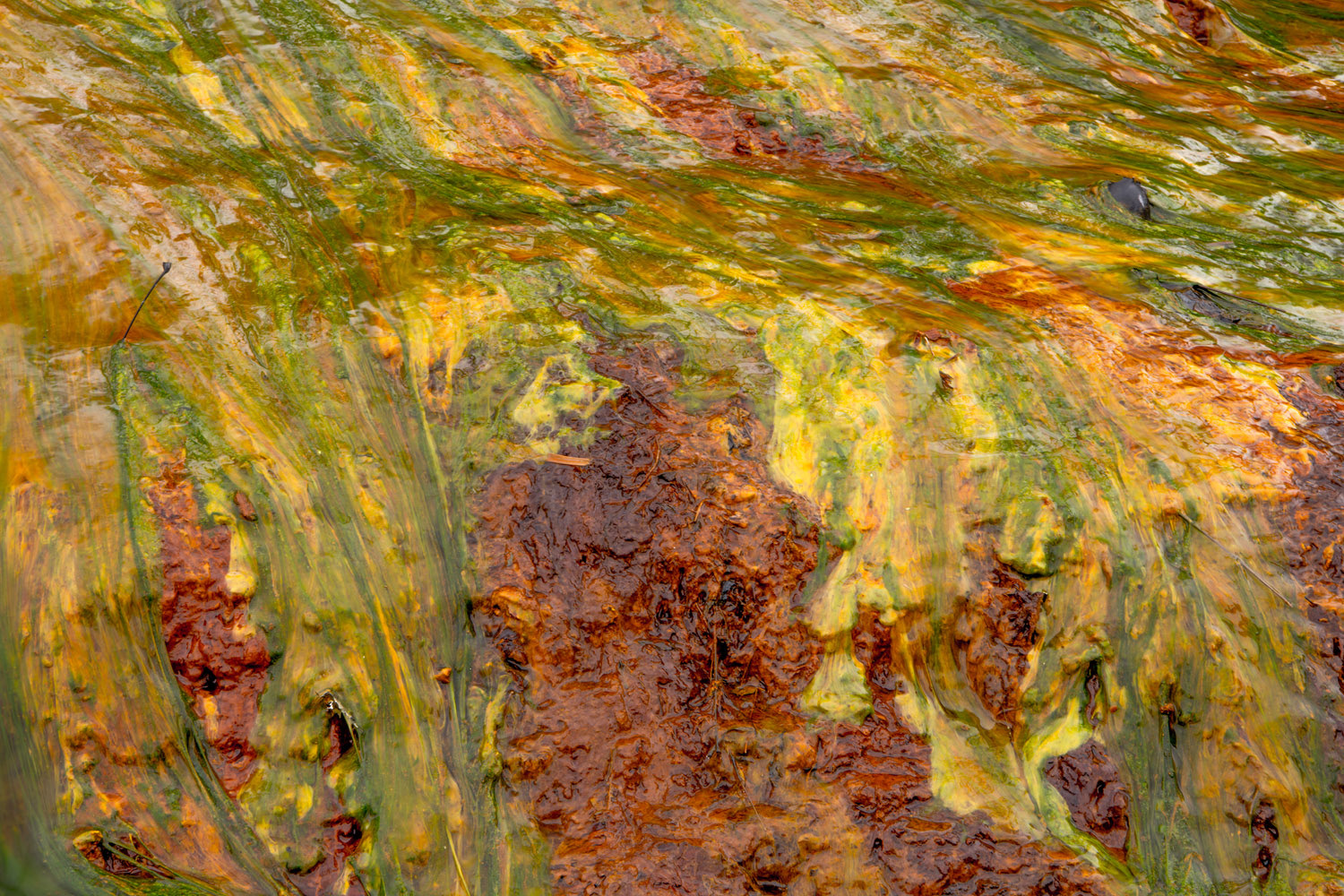
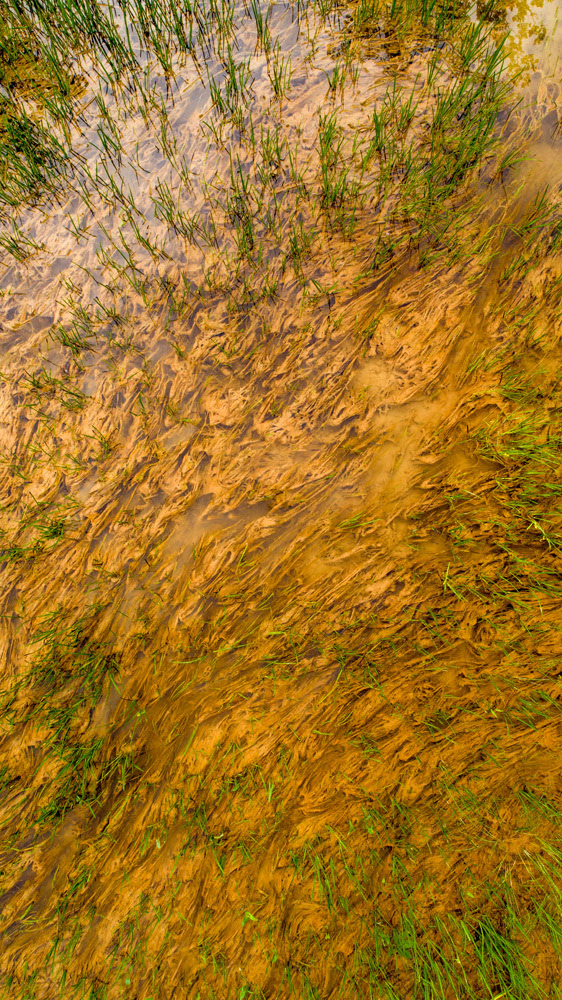
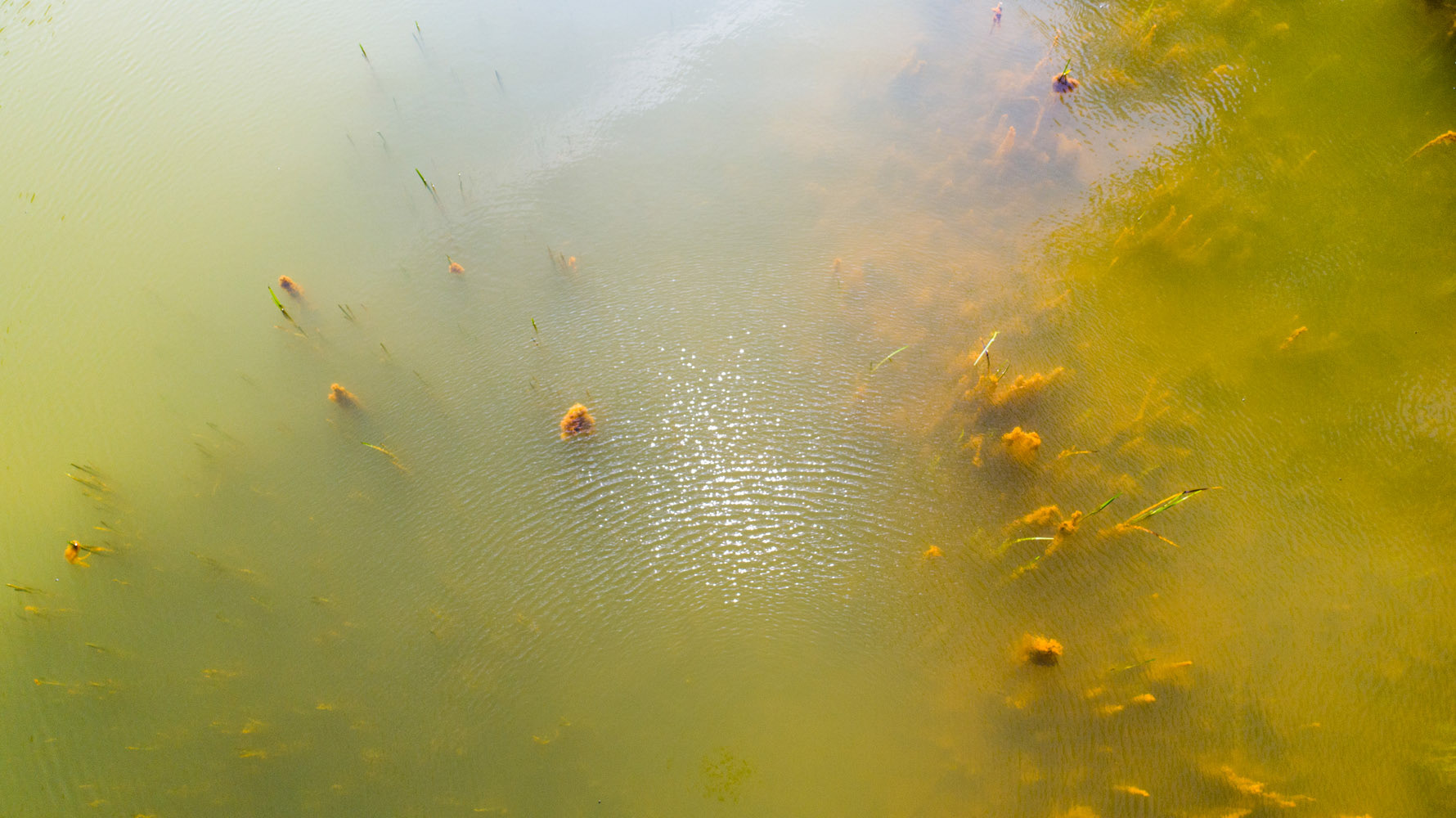
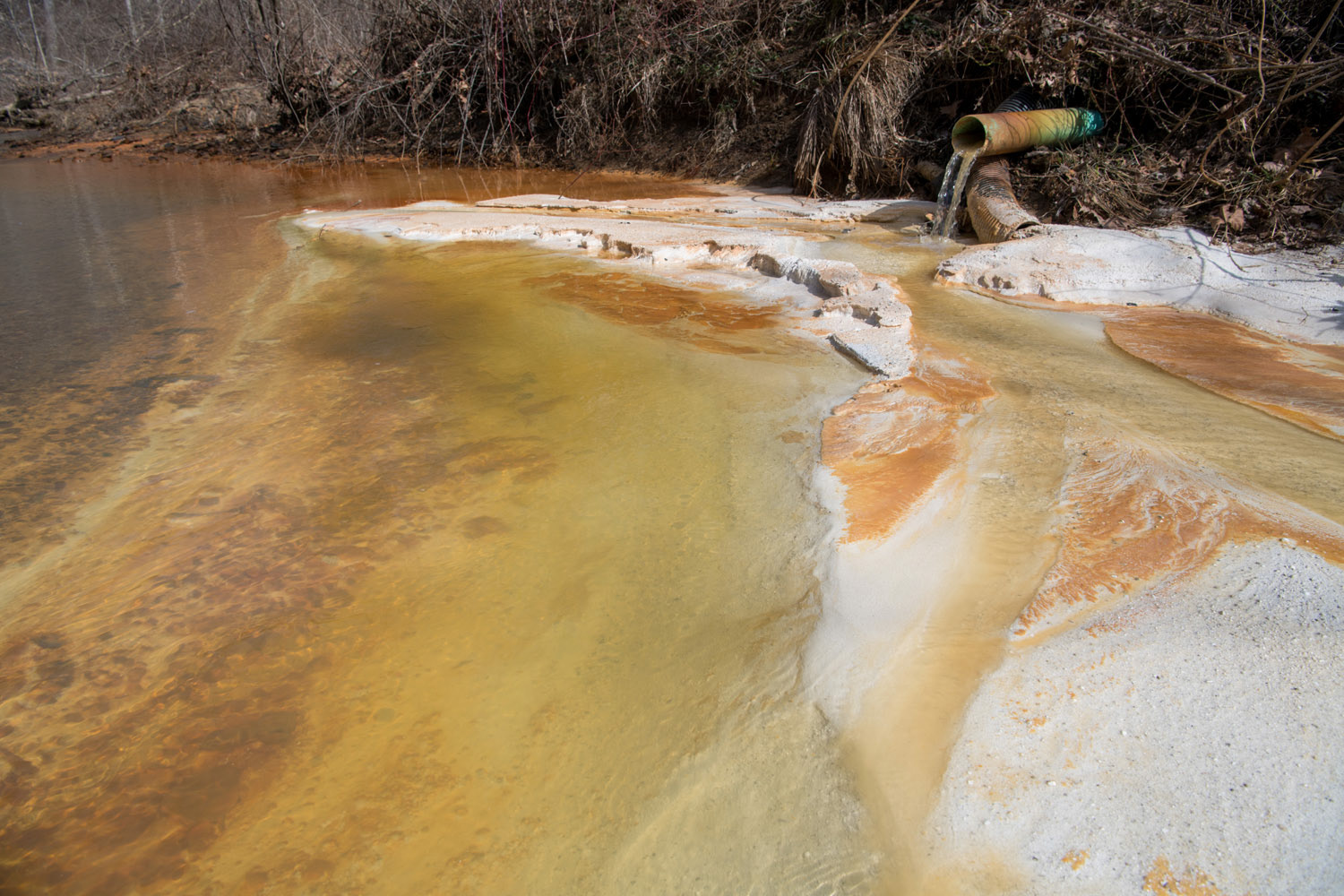
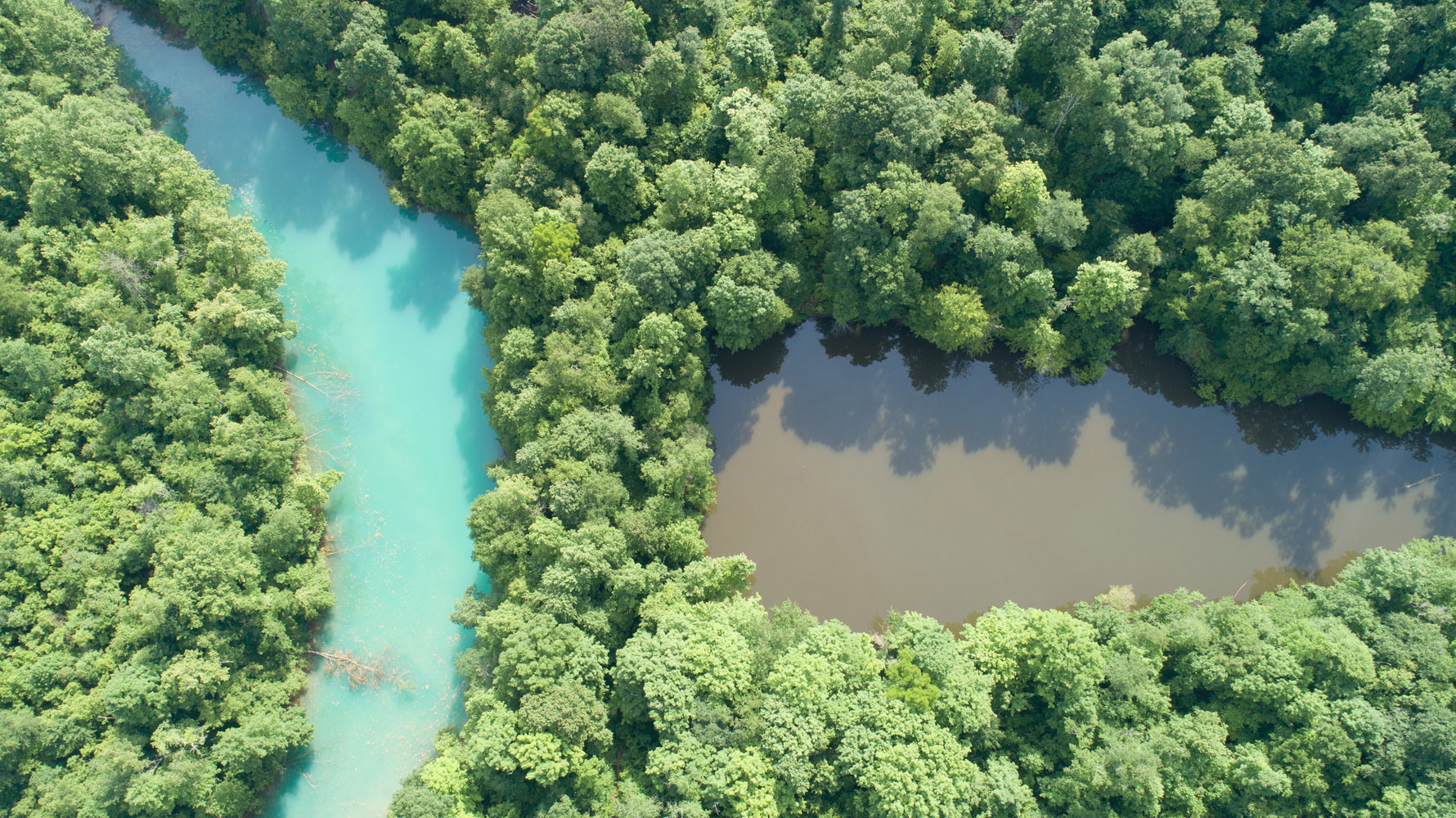
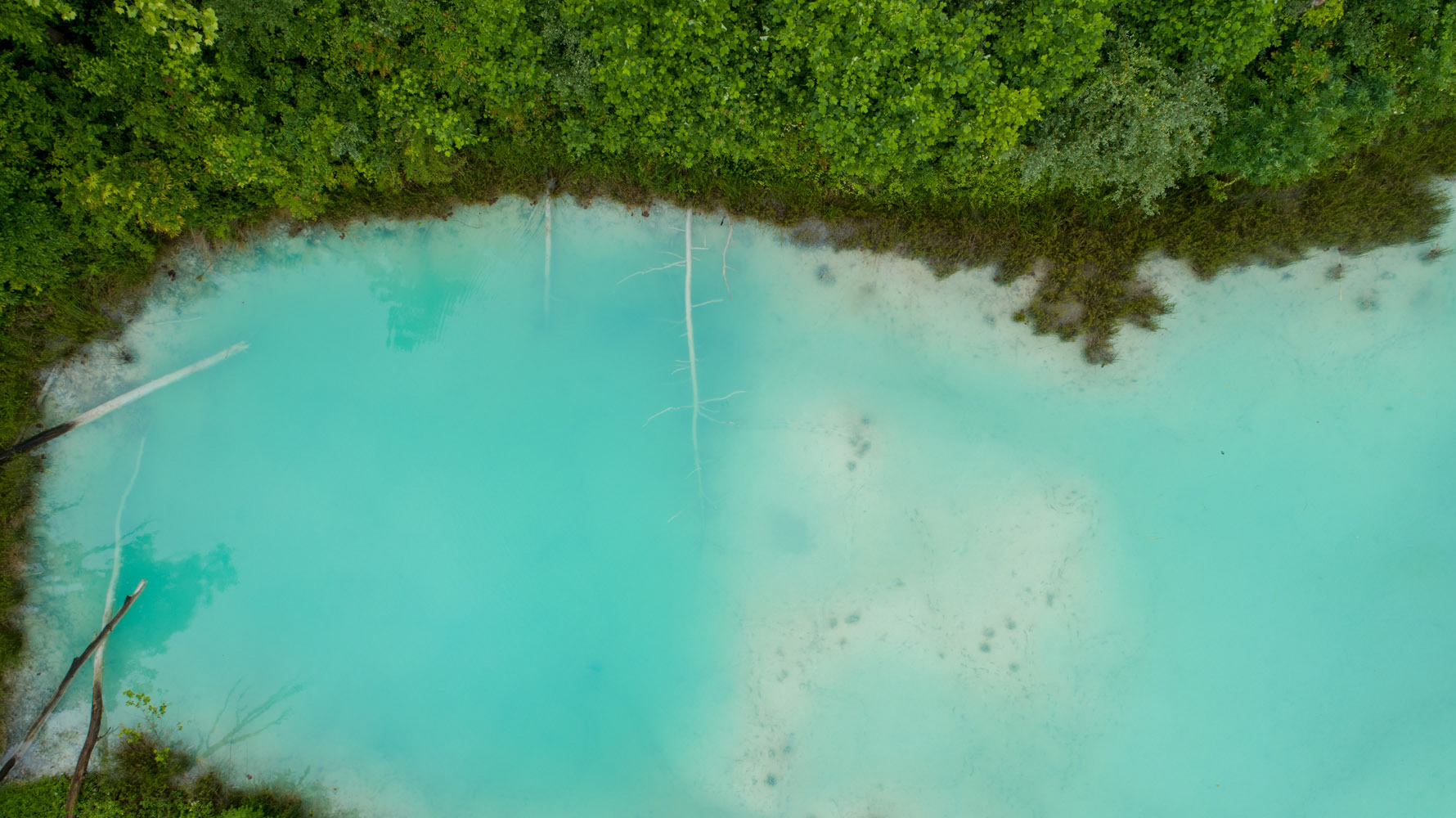
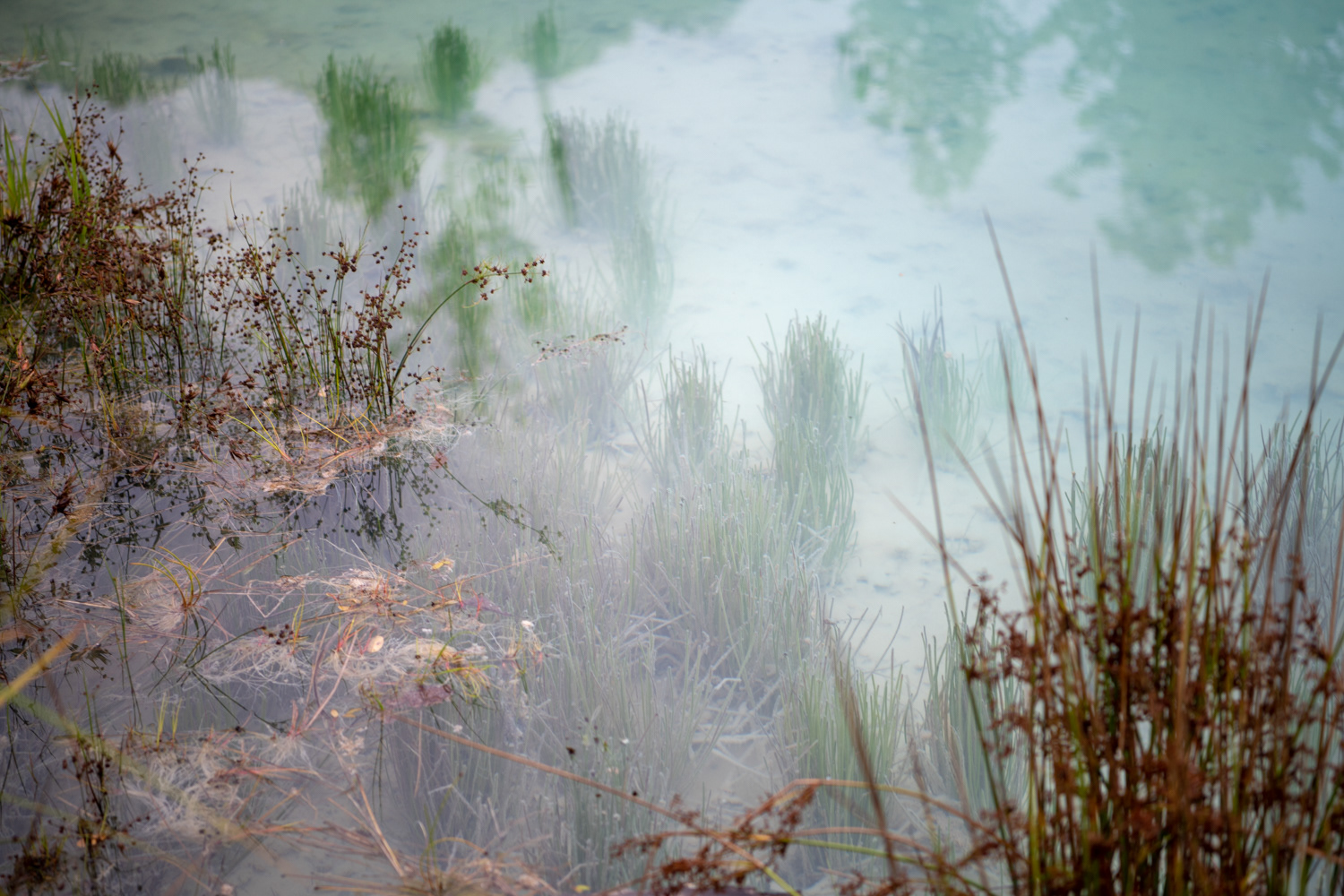
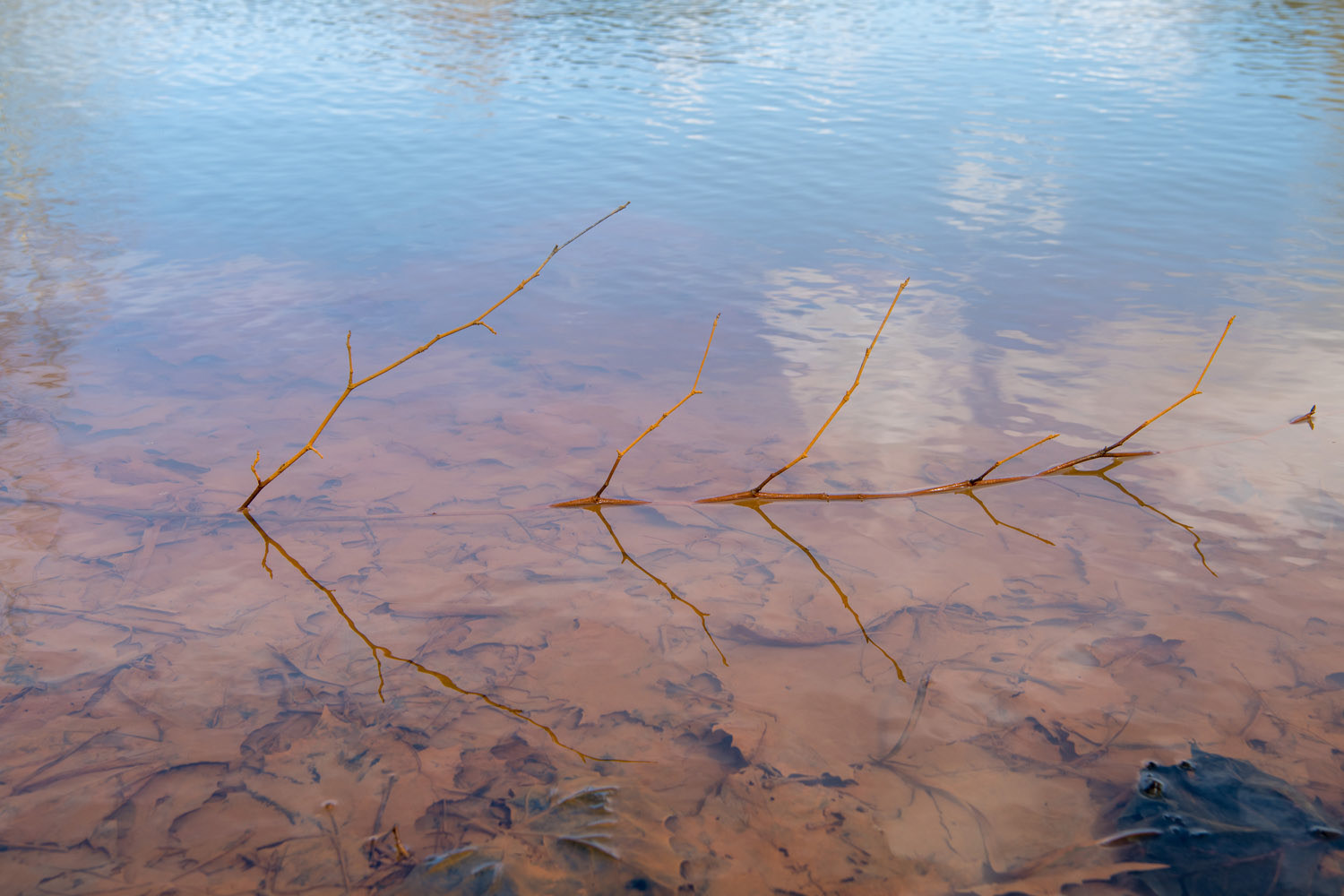
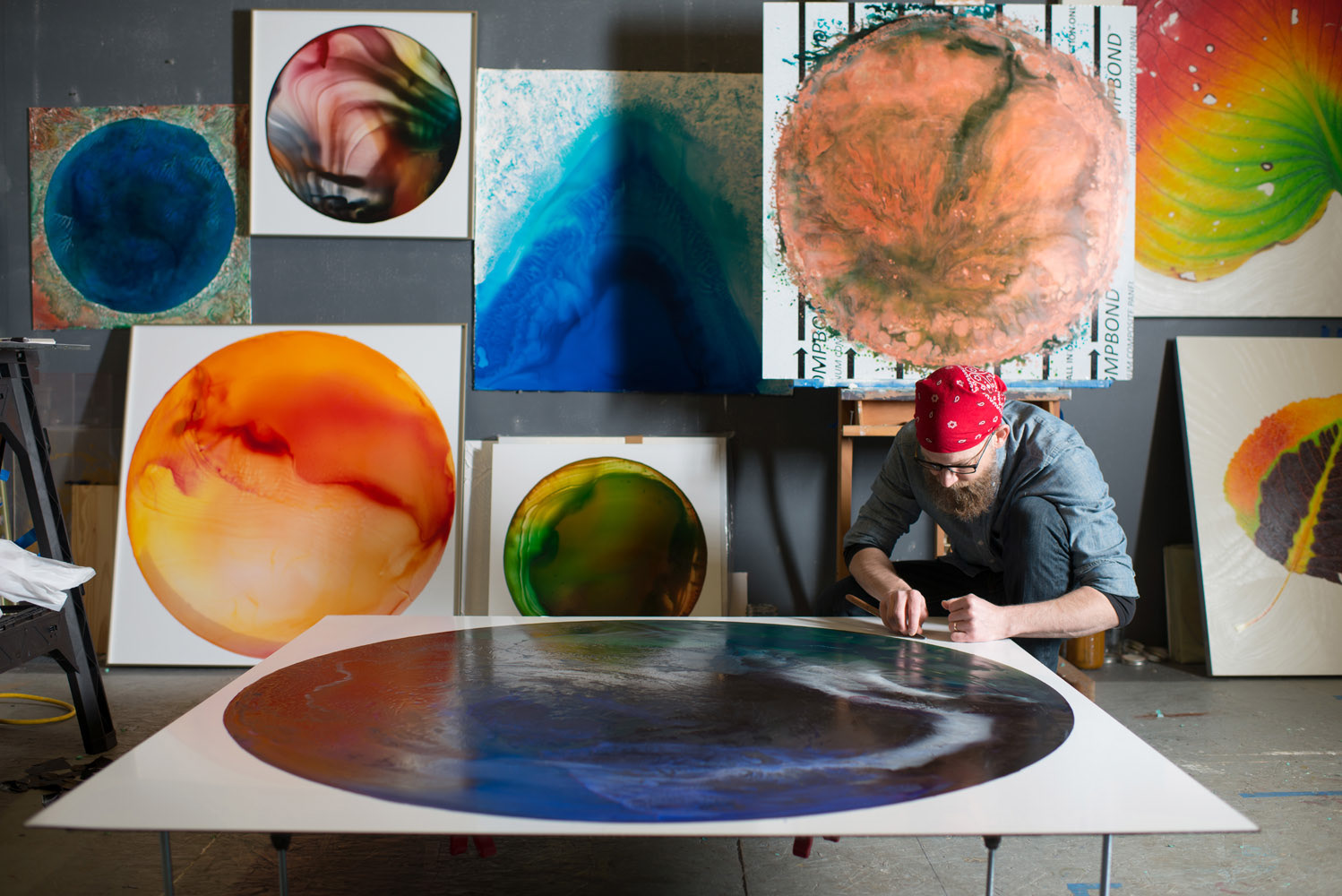
ENGINEERING MEETS FINE ARTS
“It wasn’t really until I got an artist involved that things started to change—that’s when the project really started to get traction,” Riefler told an audience of university and community members at the Ohio University Science Café talk. That artist was Sabraw, who had a track record of partnering with scientists, promoting sustainable art practices, and using creative work to spark dialogue about environmental issues. Sabraw brought his expertise in how a quality paint pigment should look and behave—what is the right texture and luminosity? How does it mix with other commercial pigments?—to the table to help perfect the paint pigment, he explained at the Science Café. The iron oxide is removed and baked at different temperatures to create different colors—the hotter the temperature, the deeper red/violet it becomes.
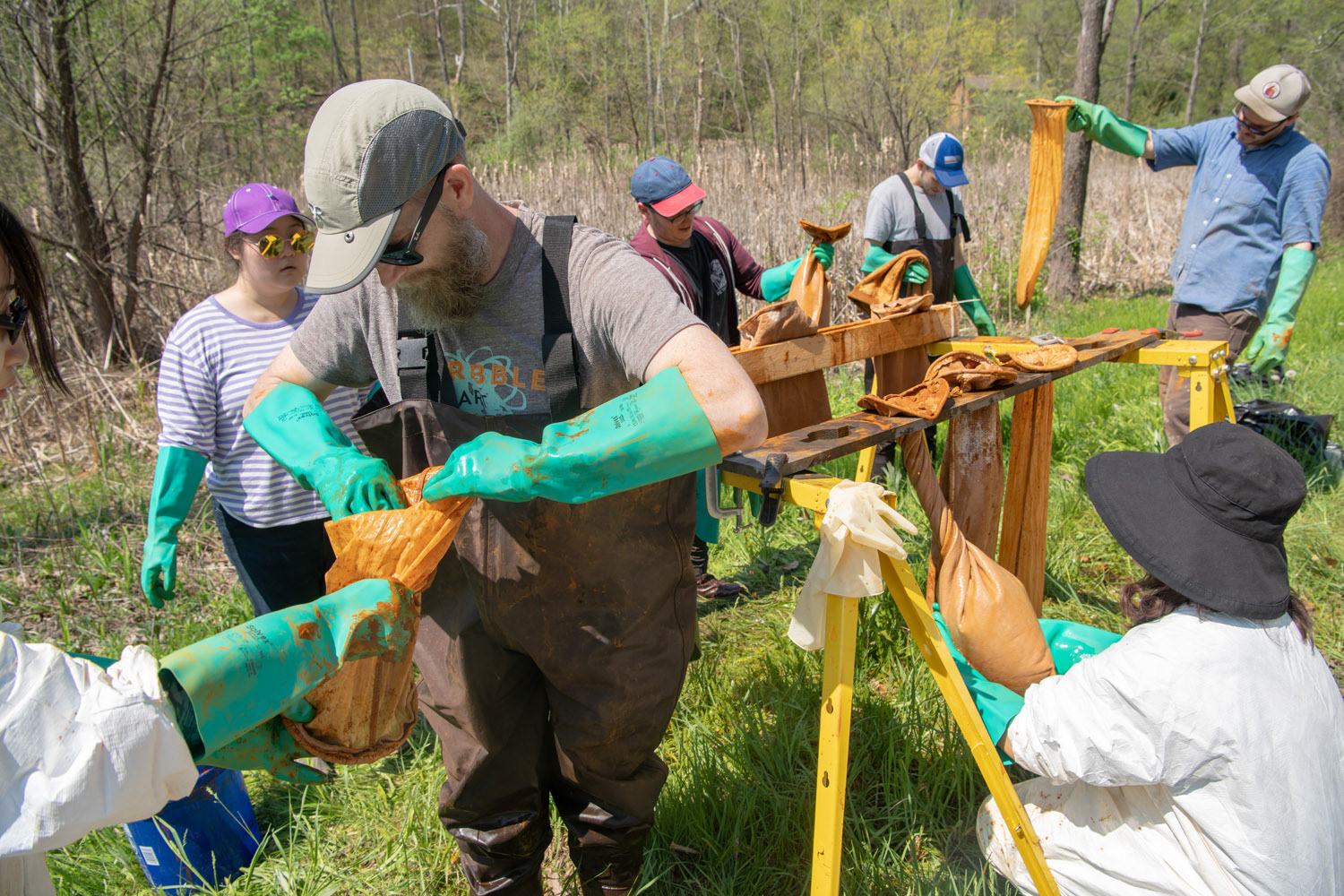
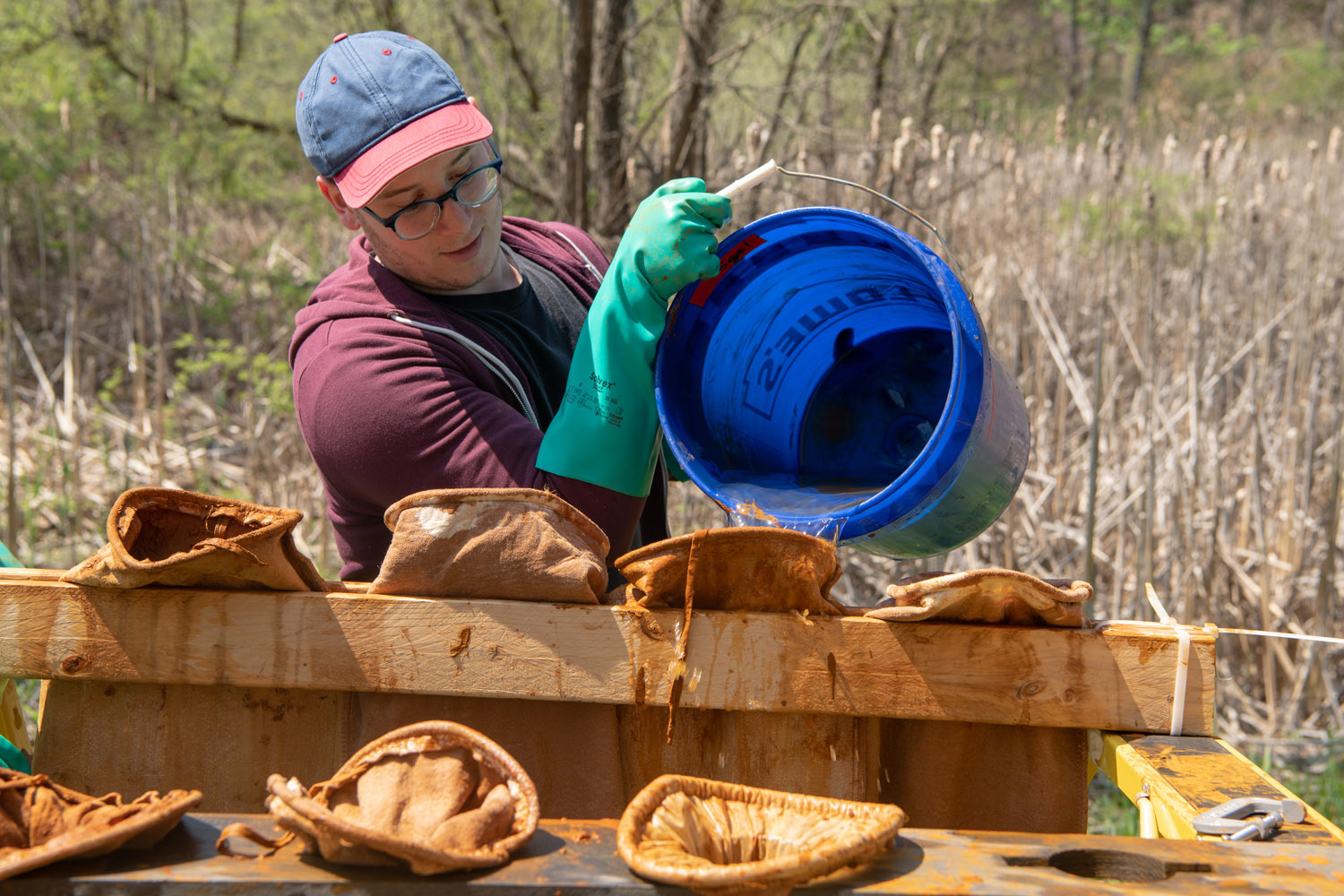
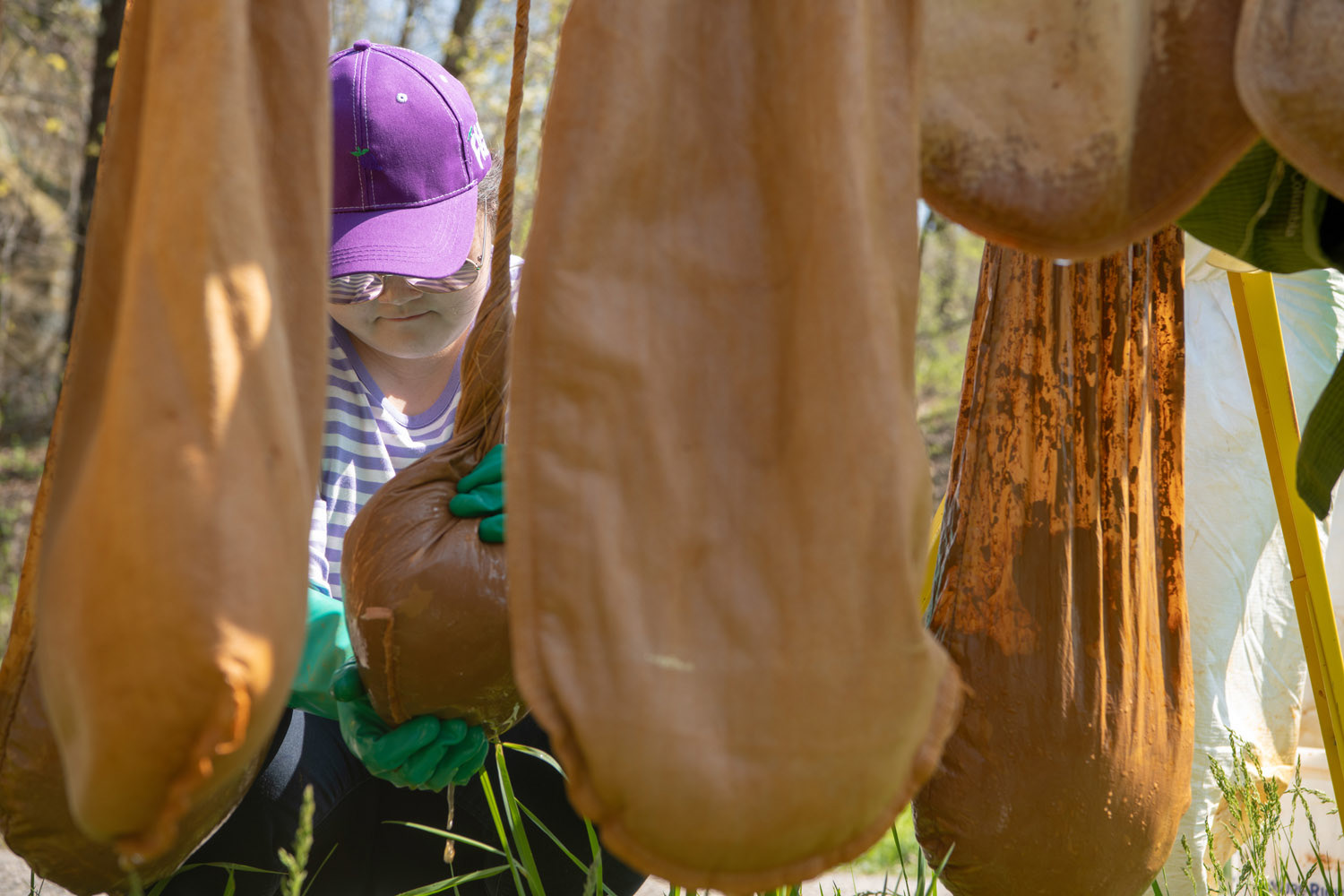
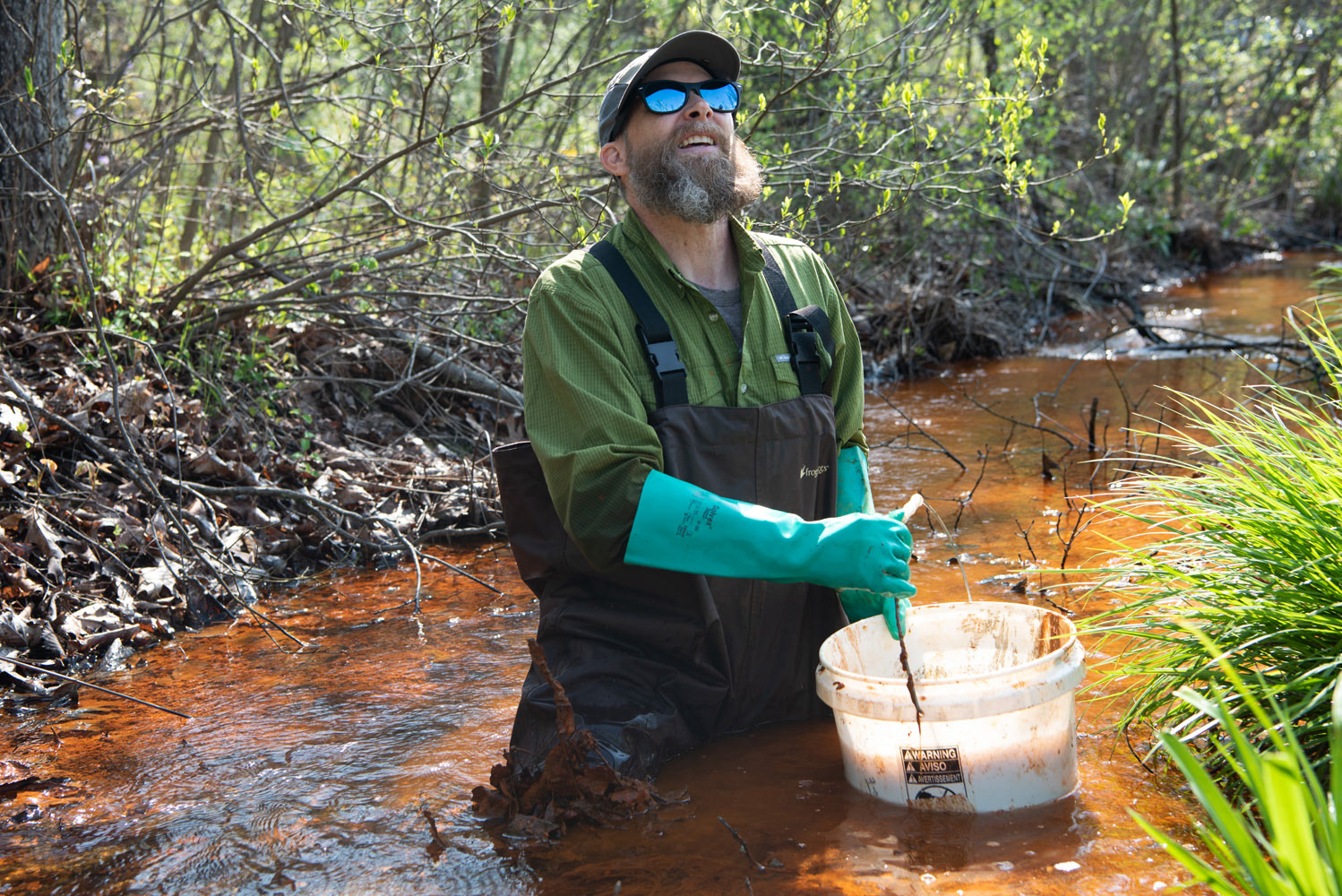
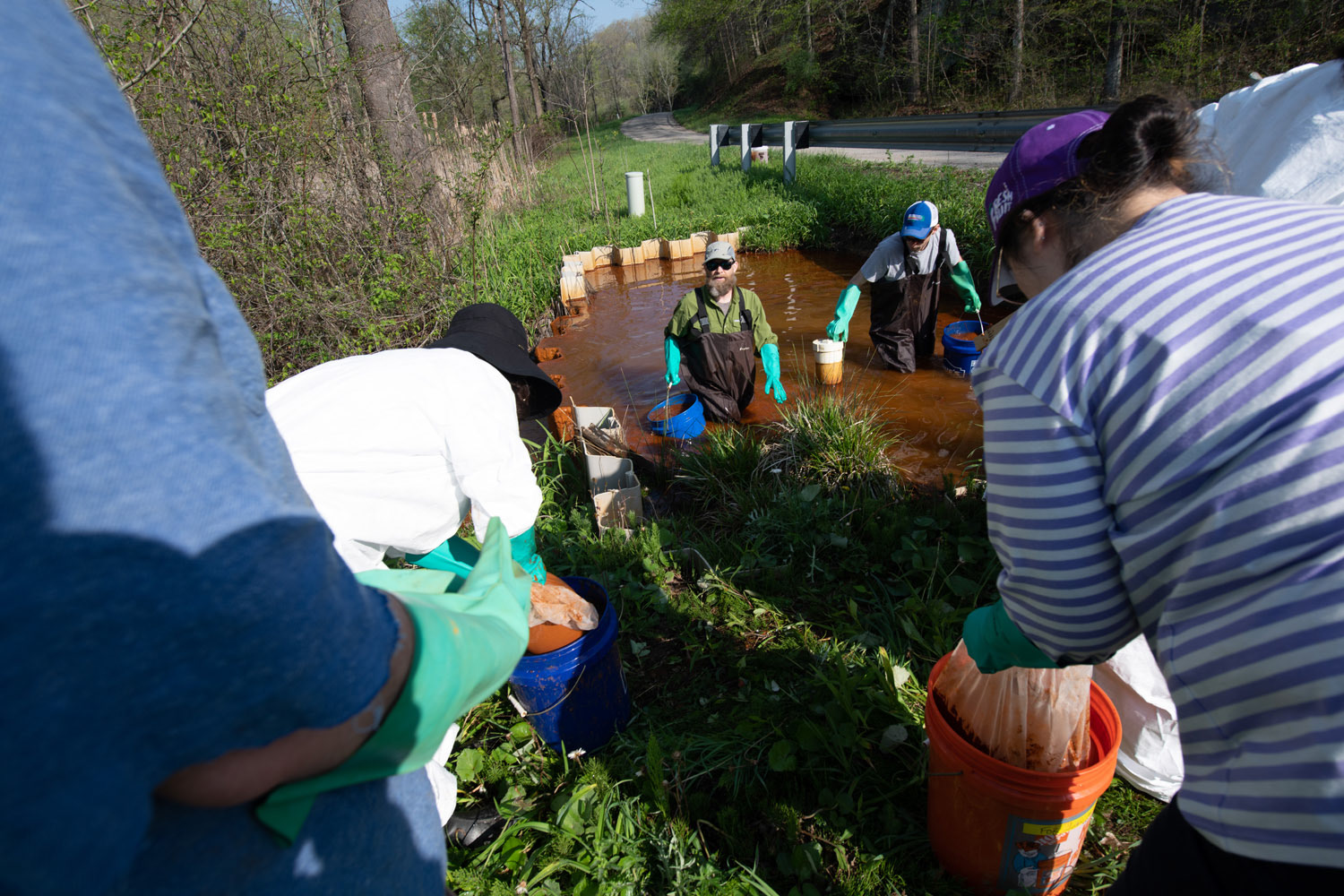
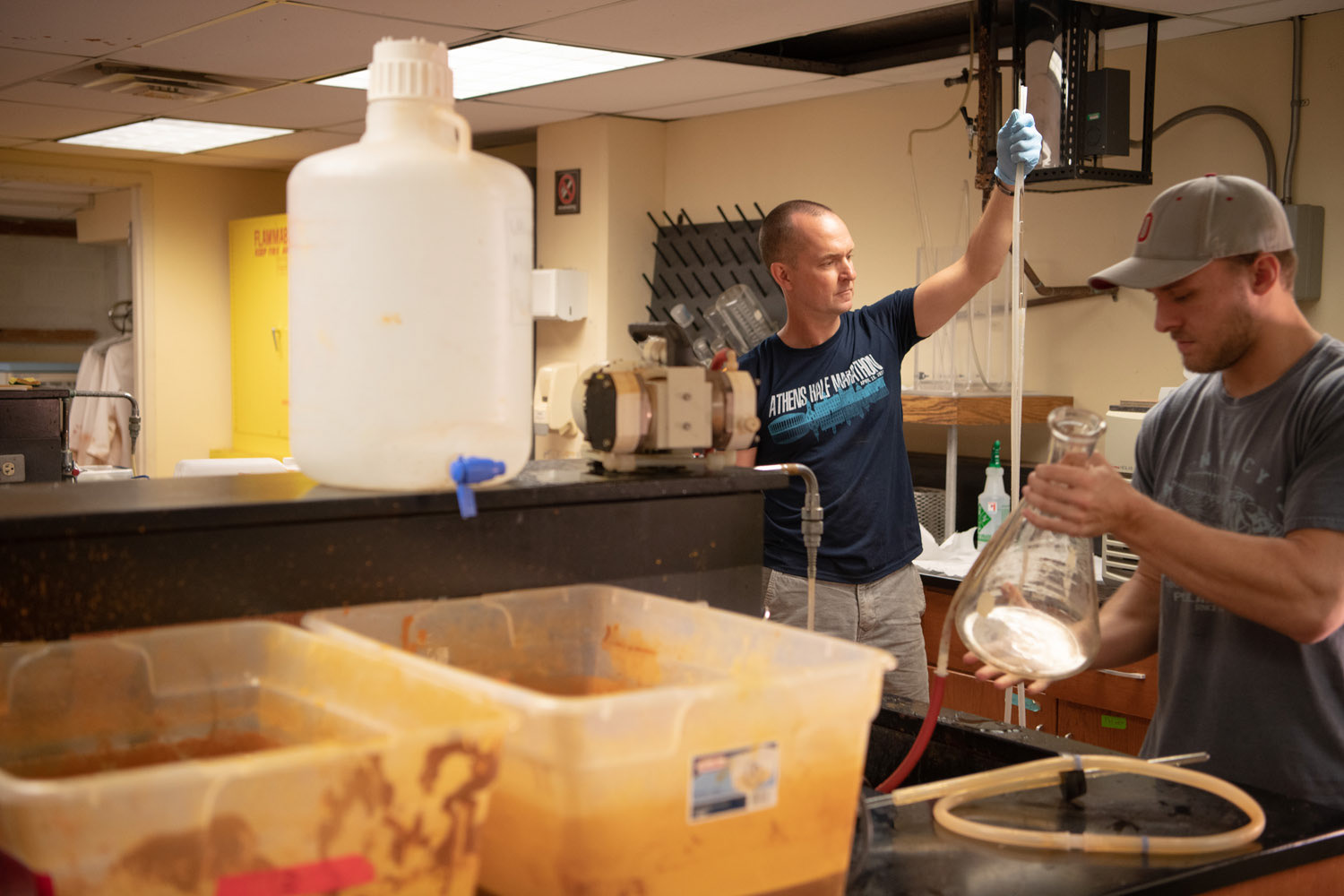
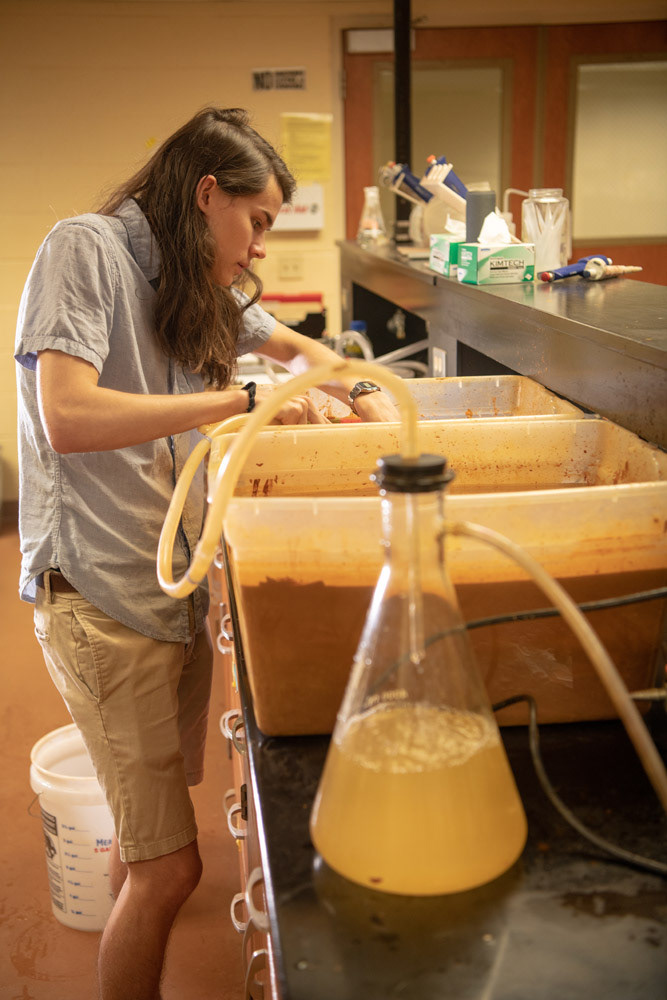
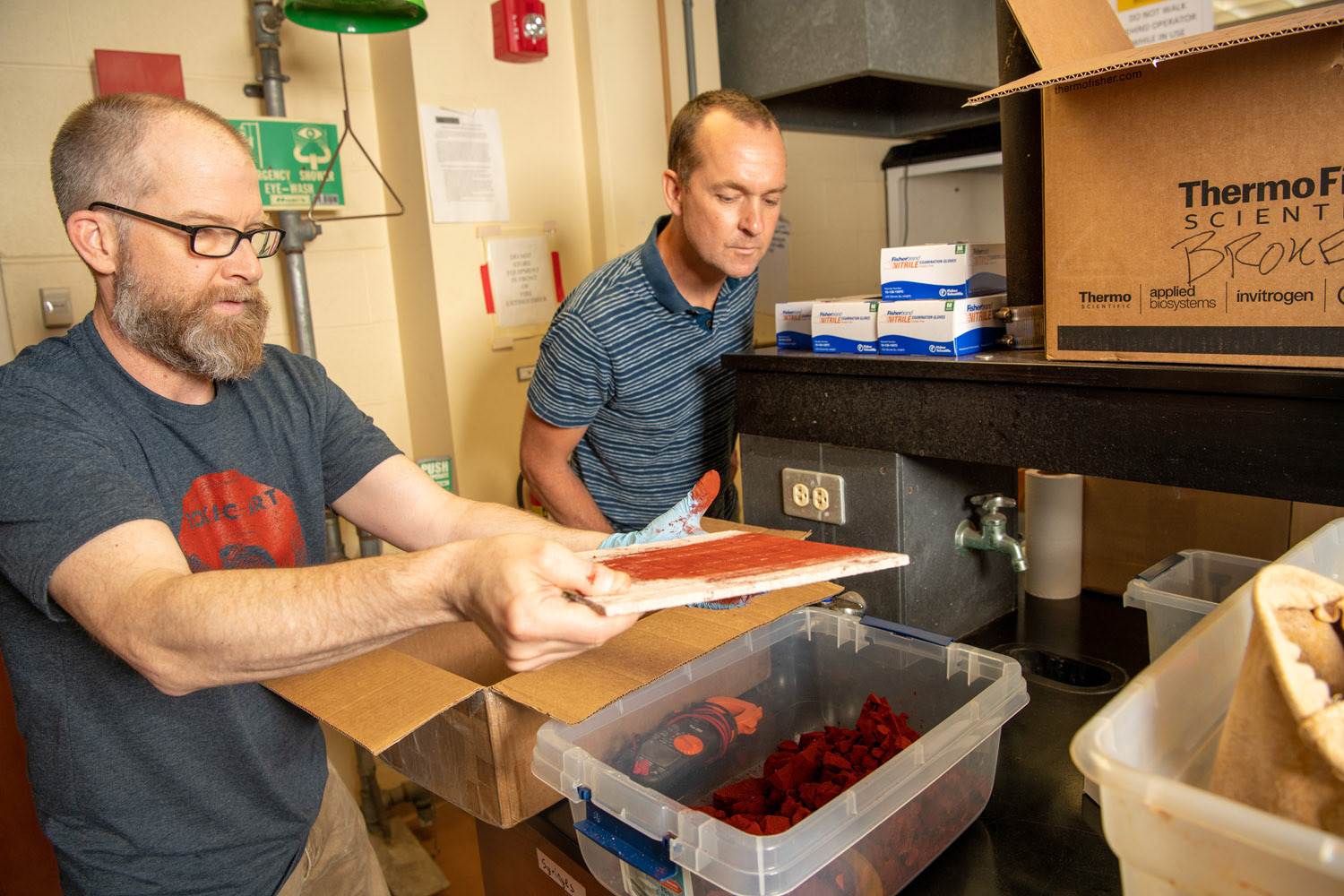
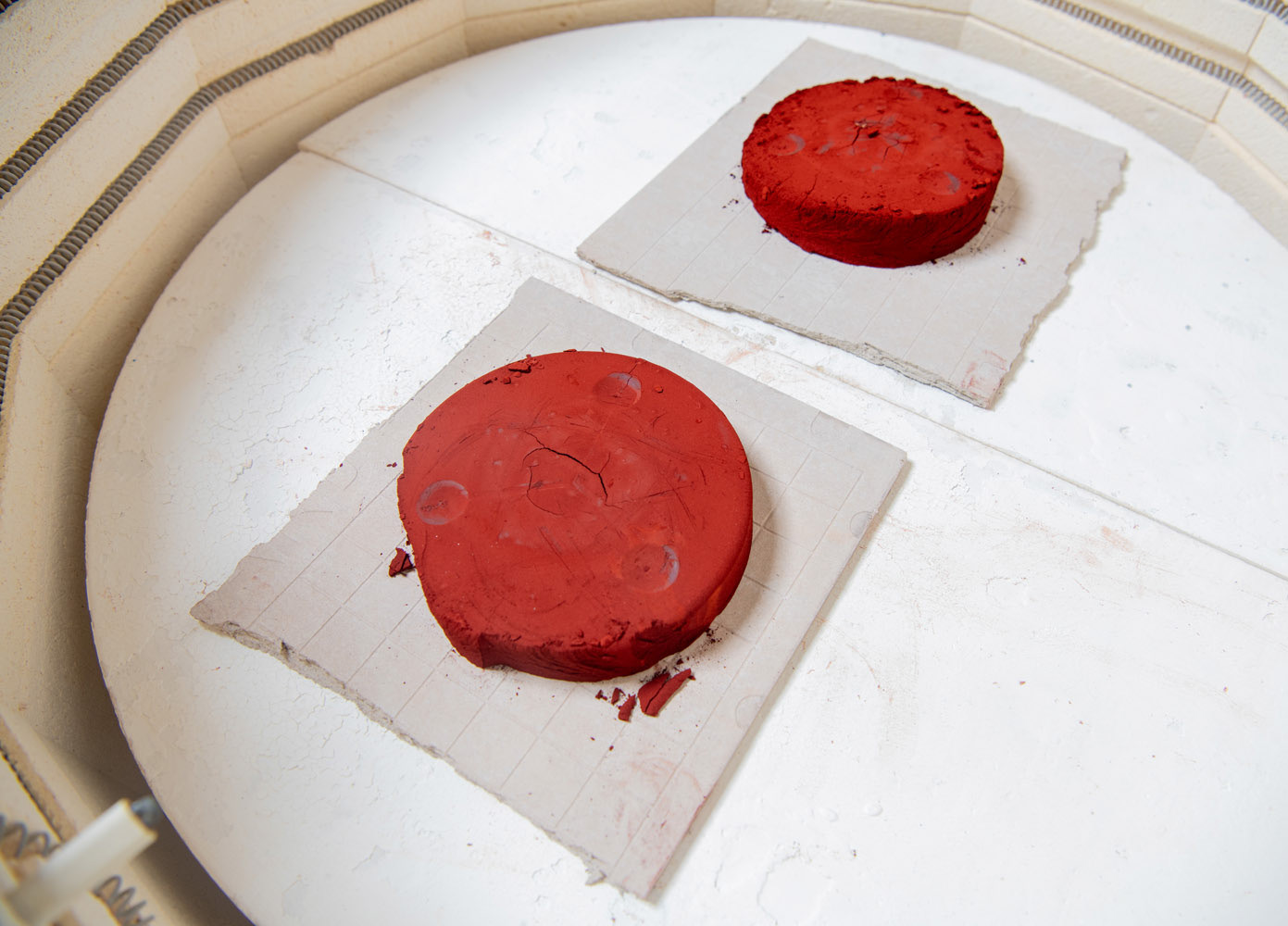
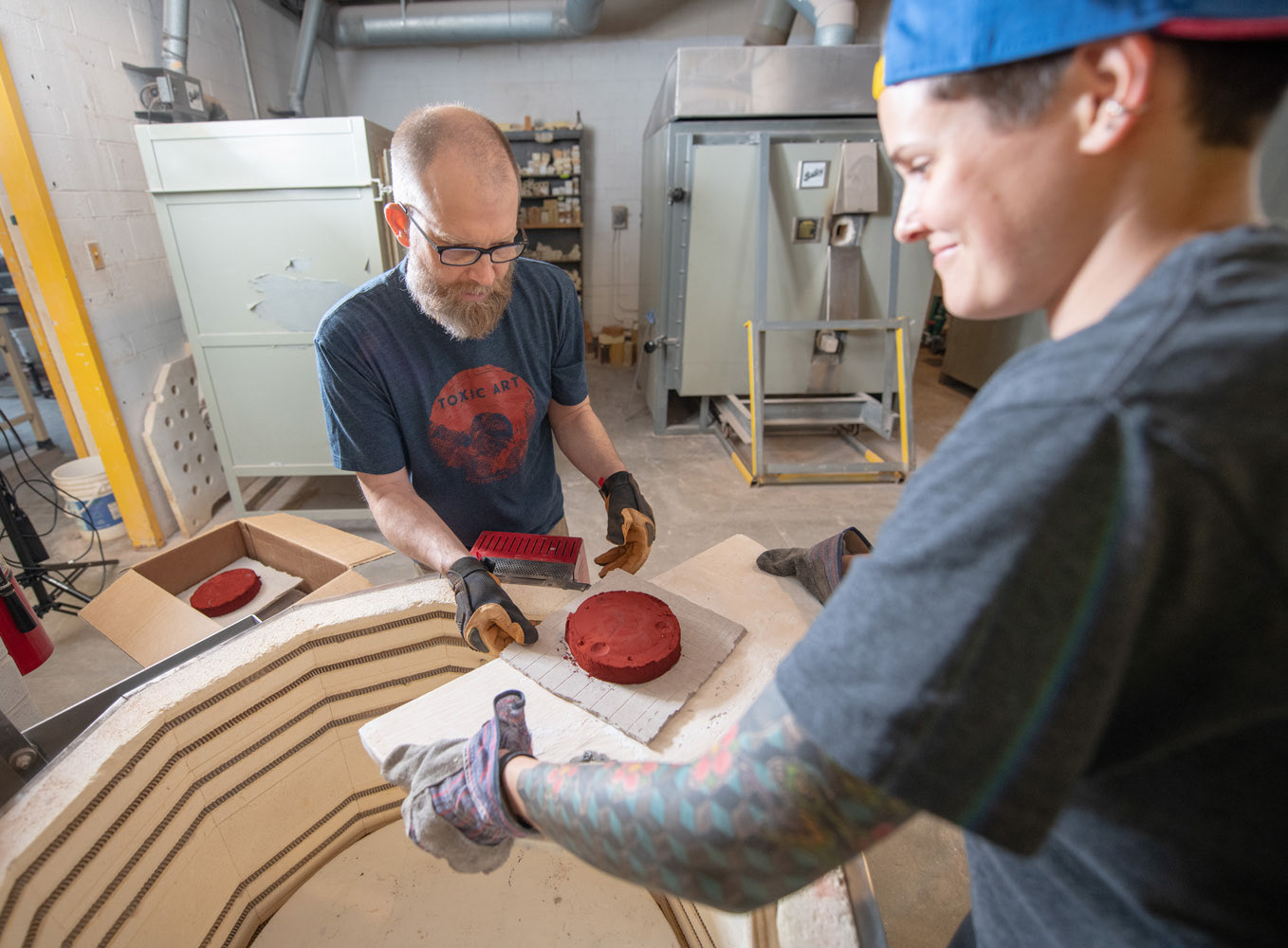
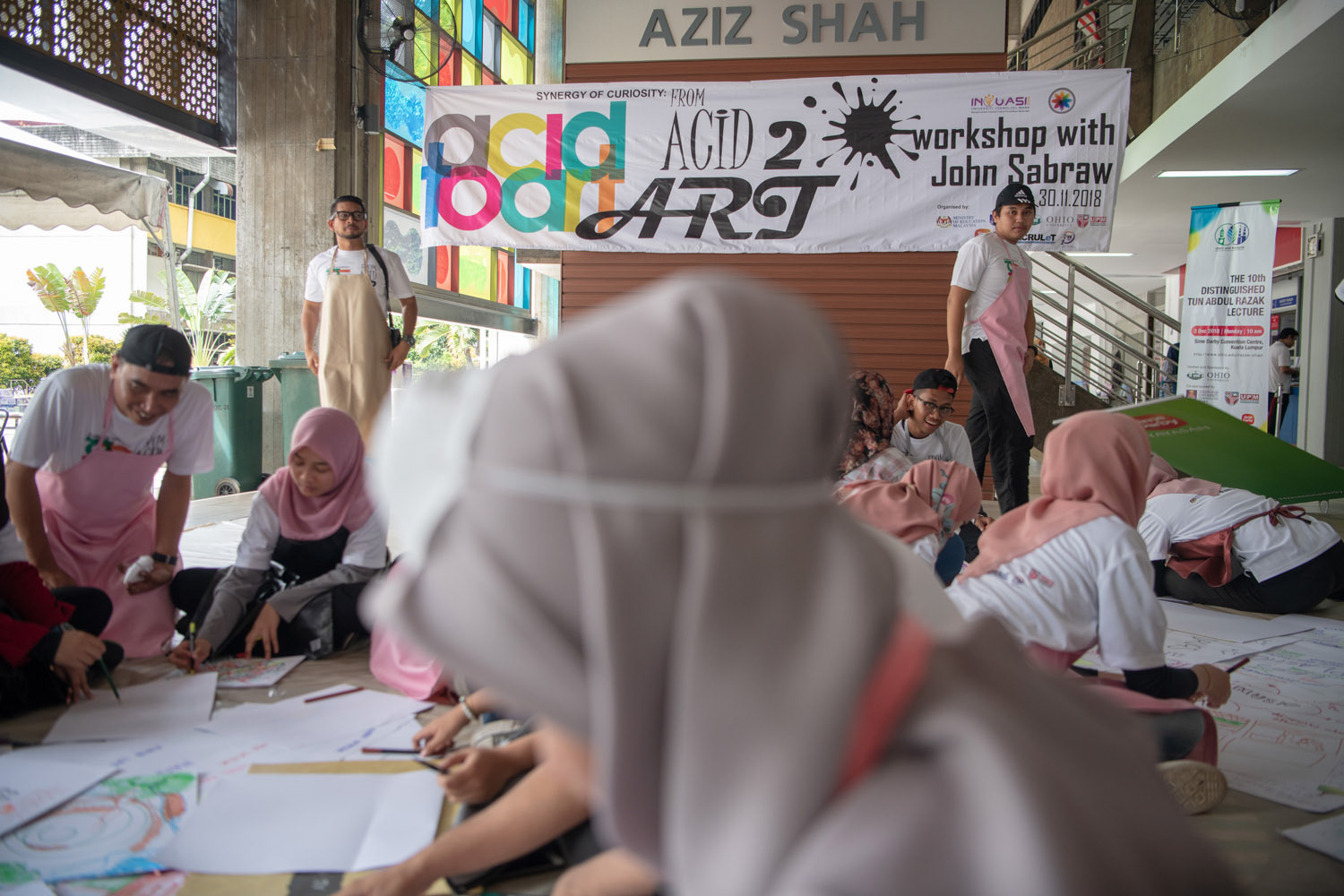
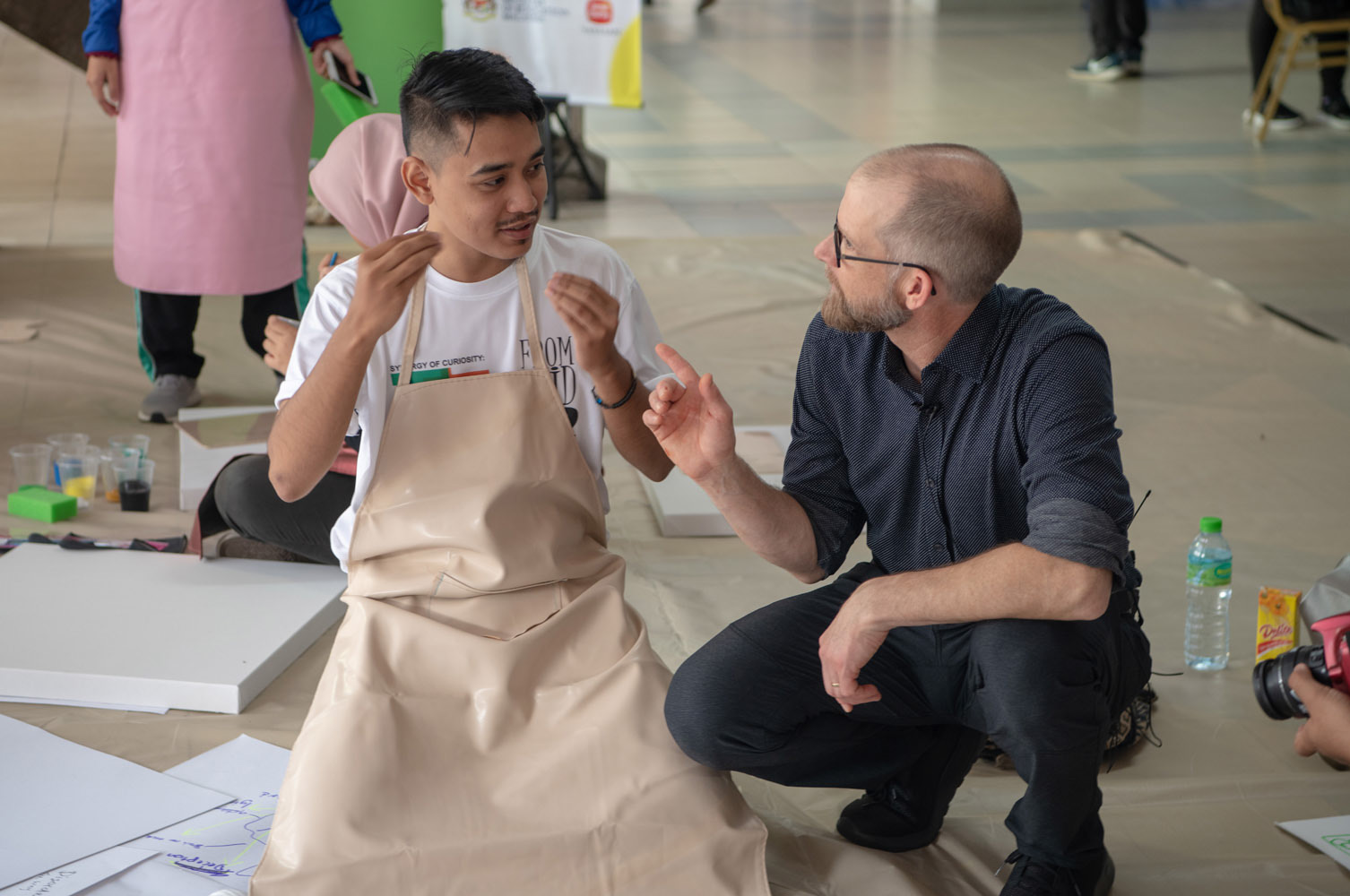
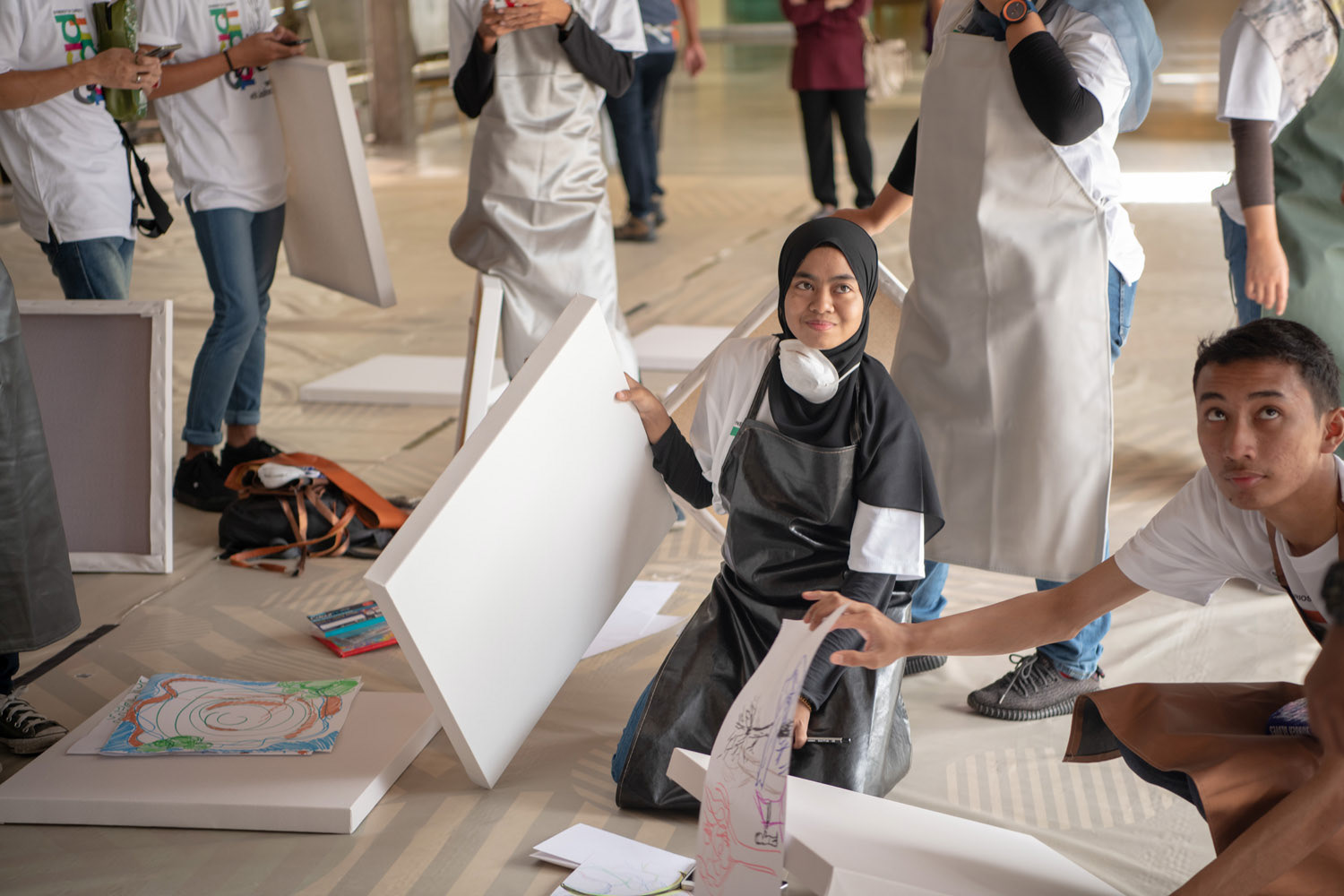
COMMUNITY PARTNERS
The Ohio University and Rural Action team have worked closely with the village council and community members of Corning, which agreed to use its public park as the site for the pilot-scale treatment facility. Like other small towns and villages in southeastern Ohio, Corning was once part of a thriving coal industry, but has struggled economically in the decades since the mines closed, Shively notes. “Turning a waste pollutant into a commodity allows us to clean up a stream in a way that not only doesn’t cost anything but adds value economically to the region,” Shively says about the benefits to the village. A full-scale facility that produces about 290,000 pounds of iron oxide could generate revenues of $217,000 in sales, which would allow a nonprofit to pay a couple of employees to run and maintain the facility, keeping the project financially sustainable while cleaning the environment, Riefler notes. “It’s a pollution remediation project at its heart—we’re trying to restore the stream,” he says.
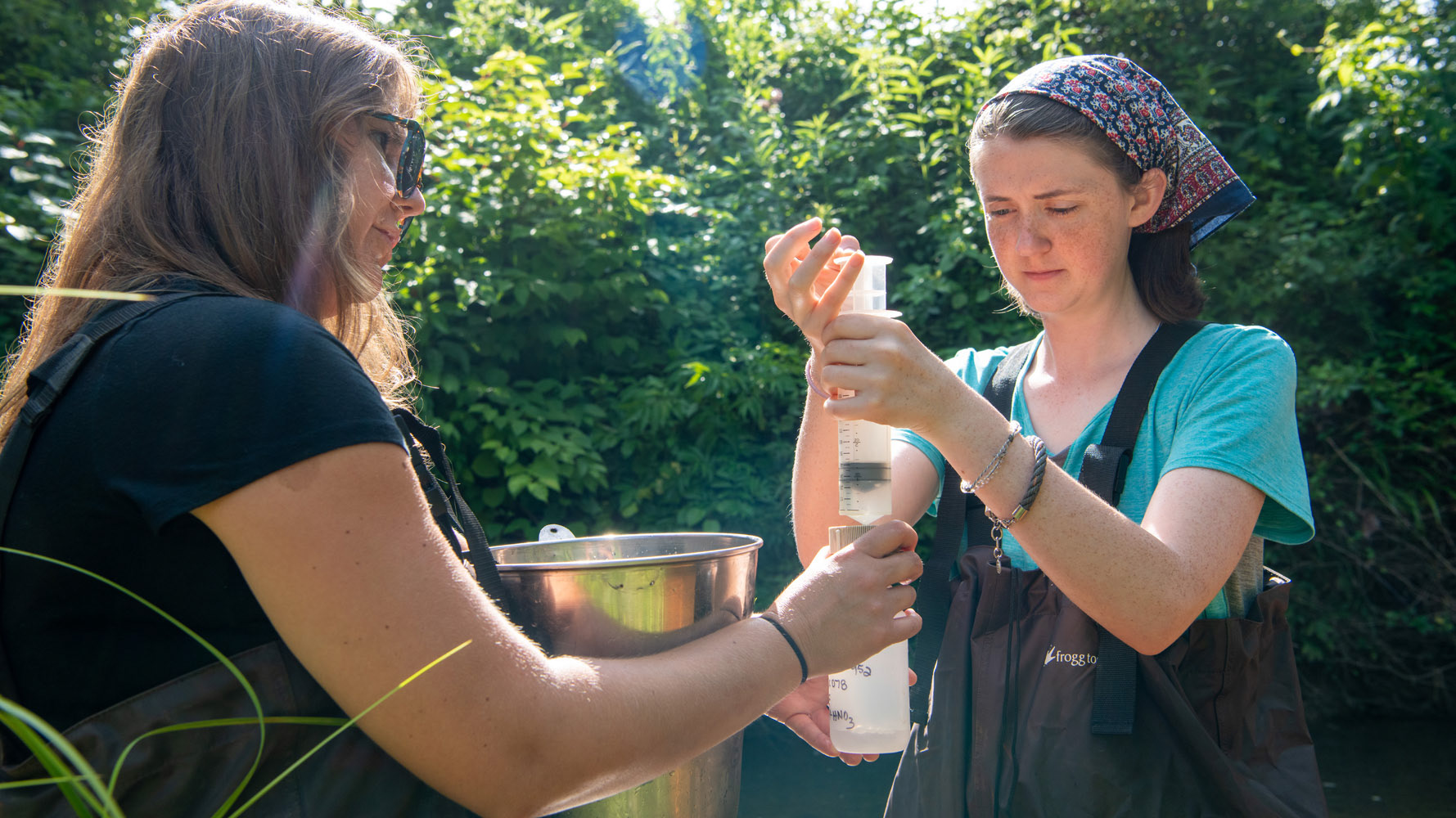
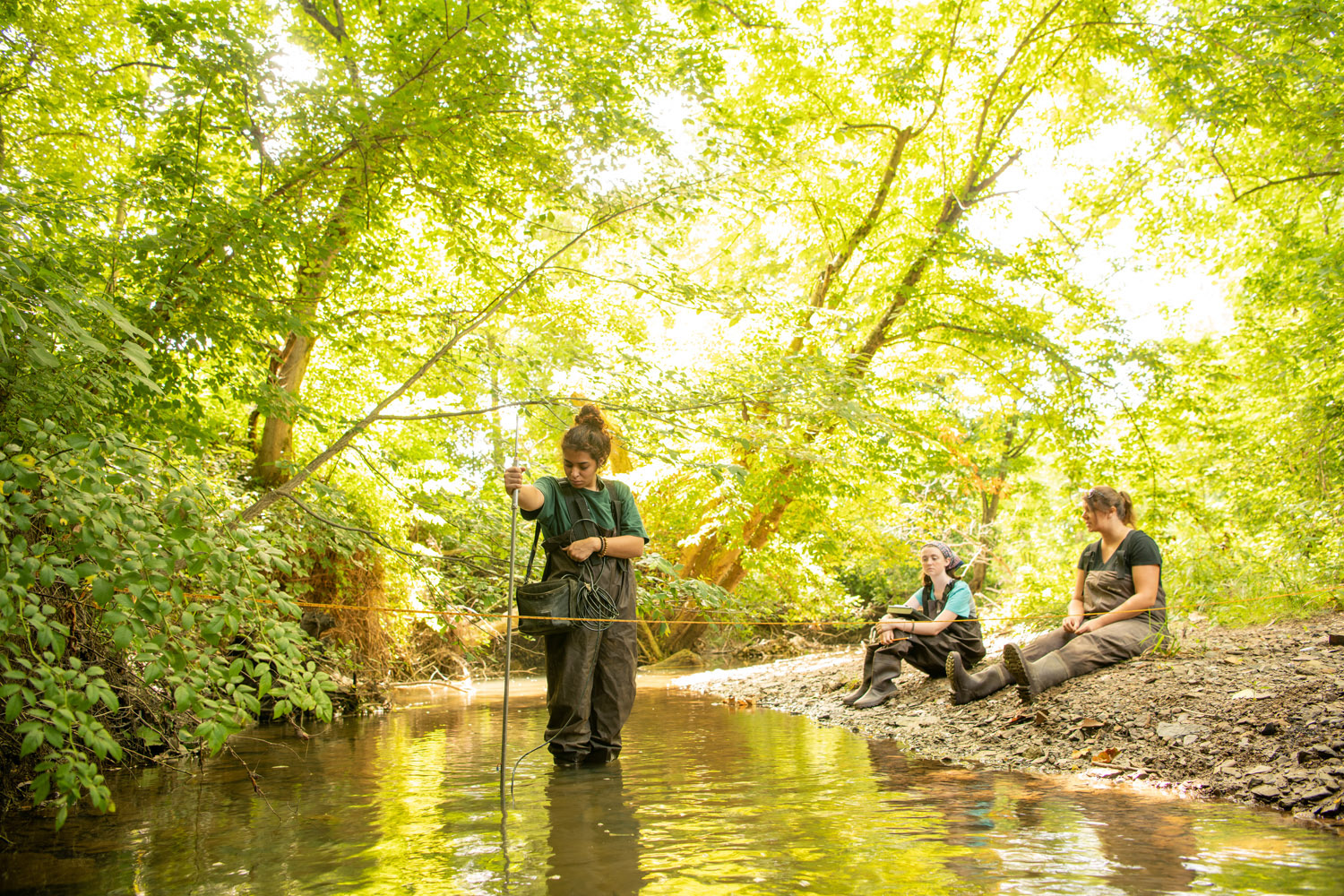
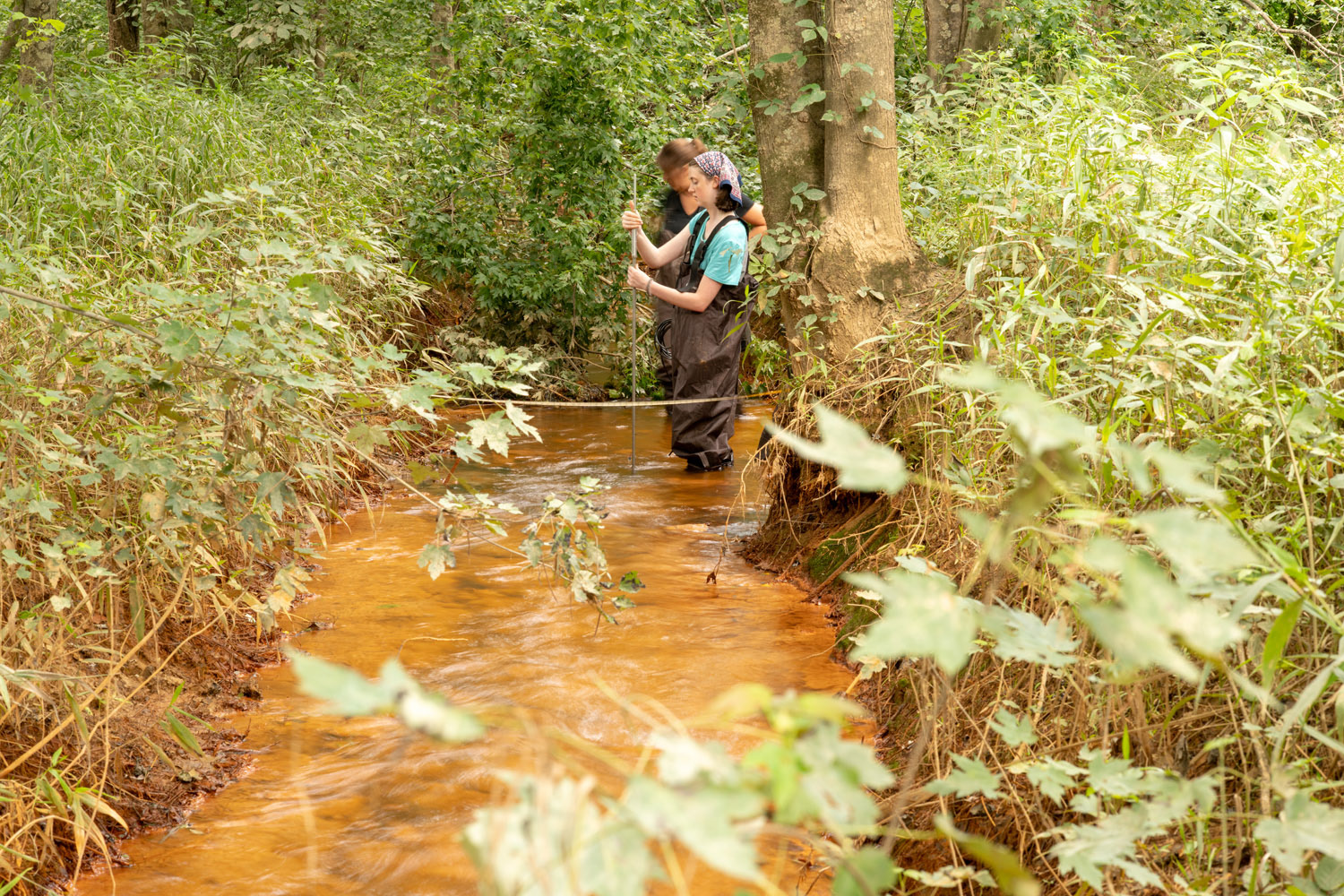
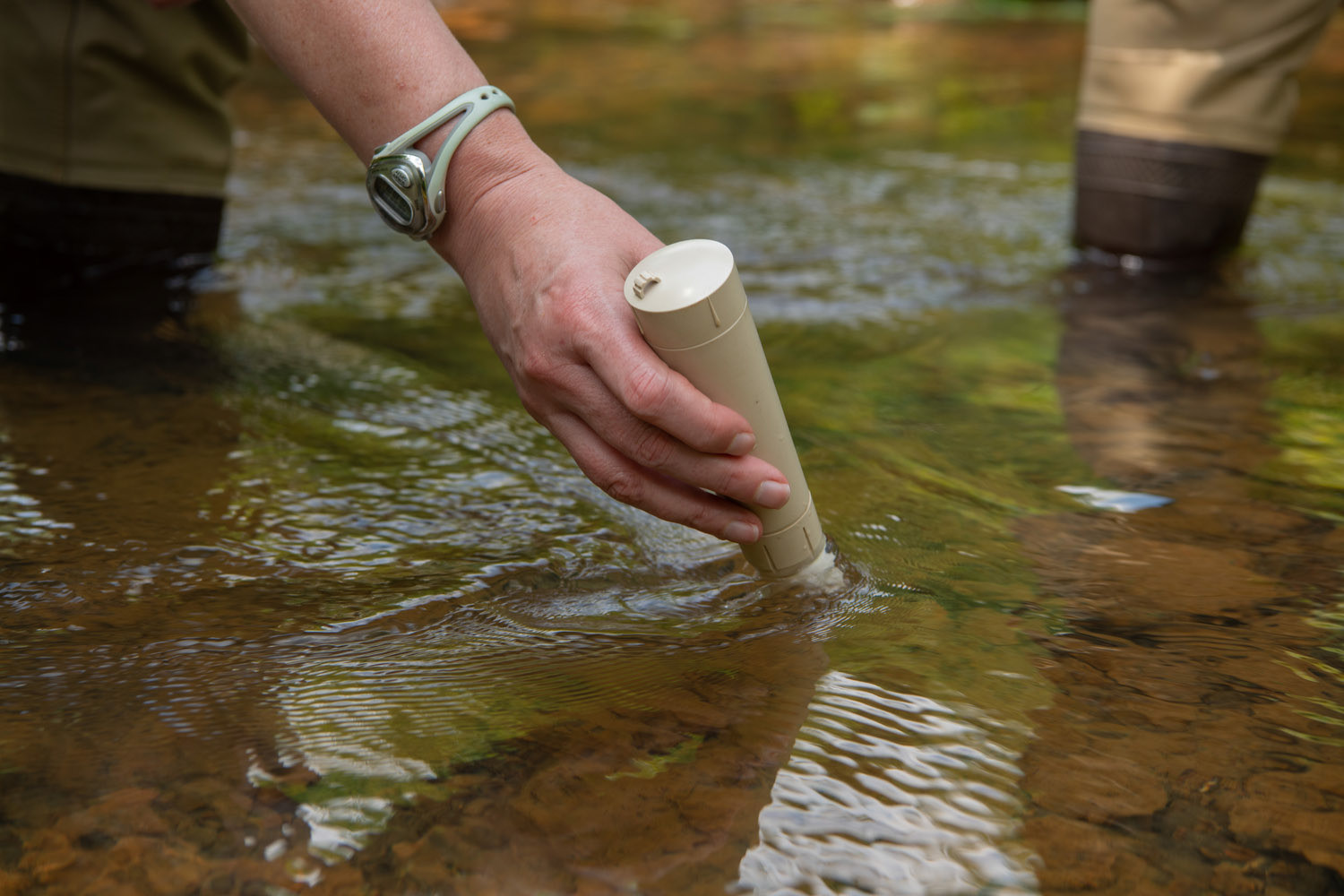
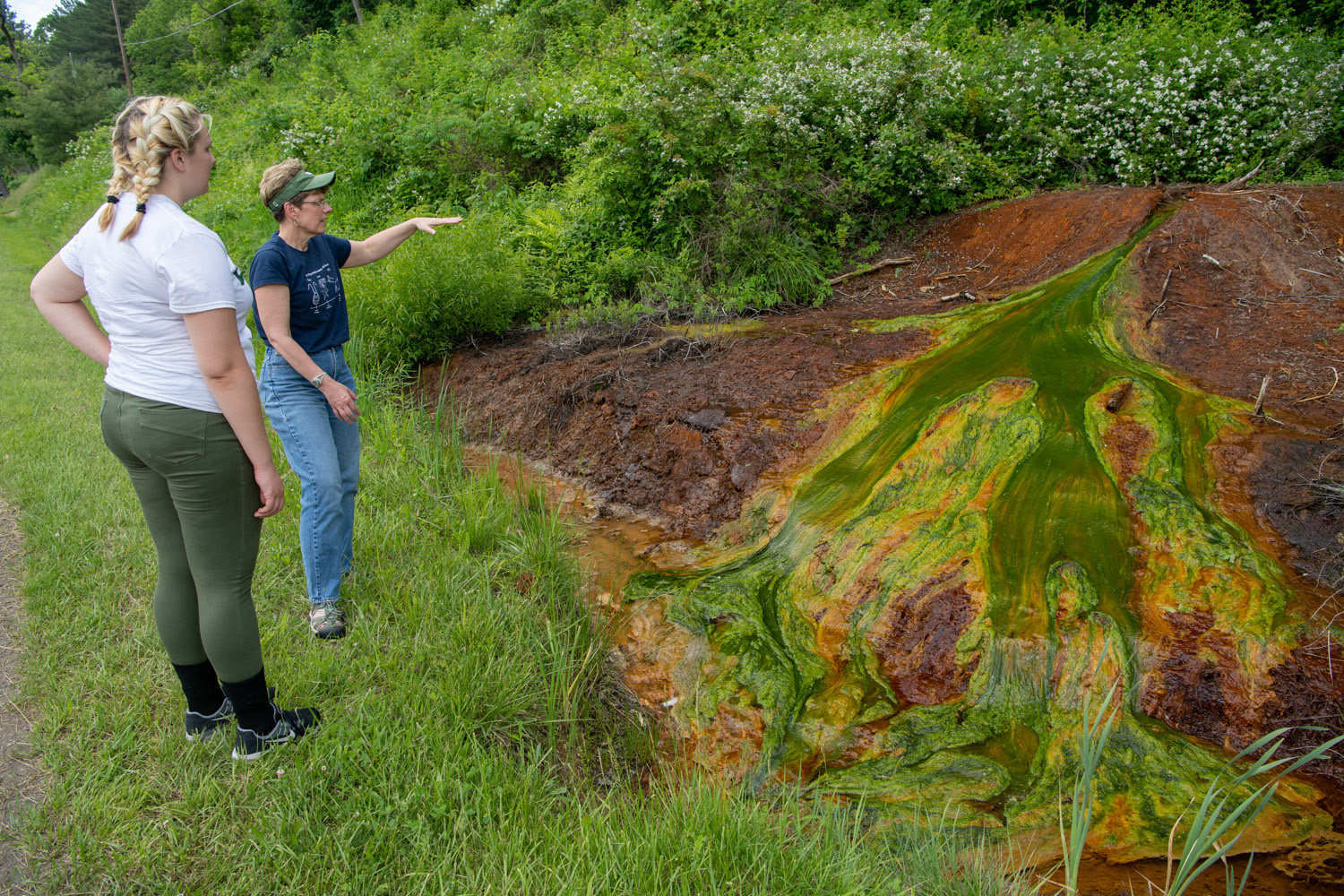
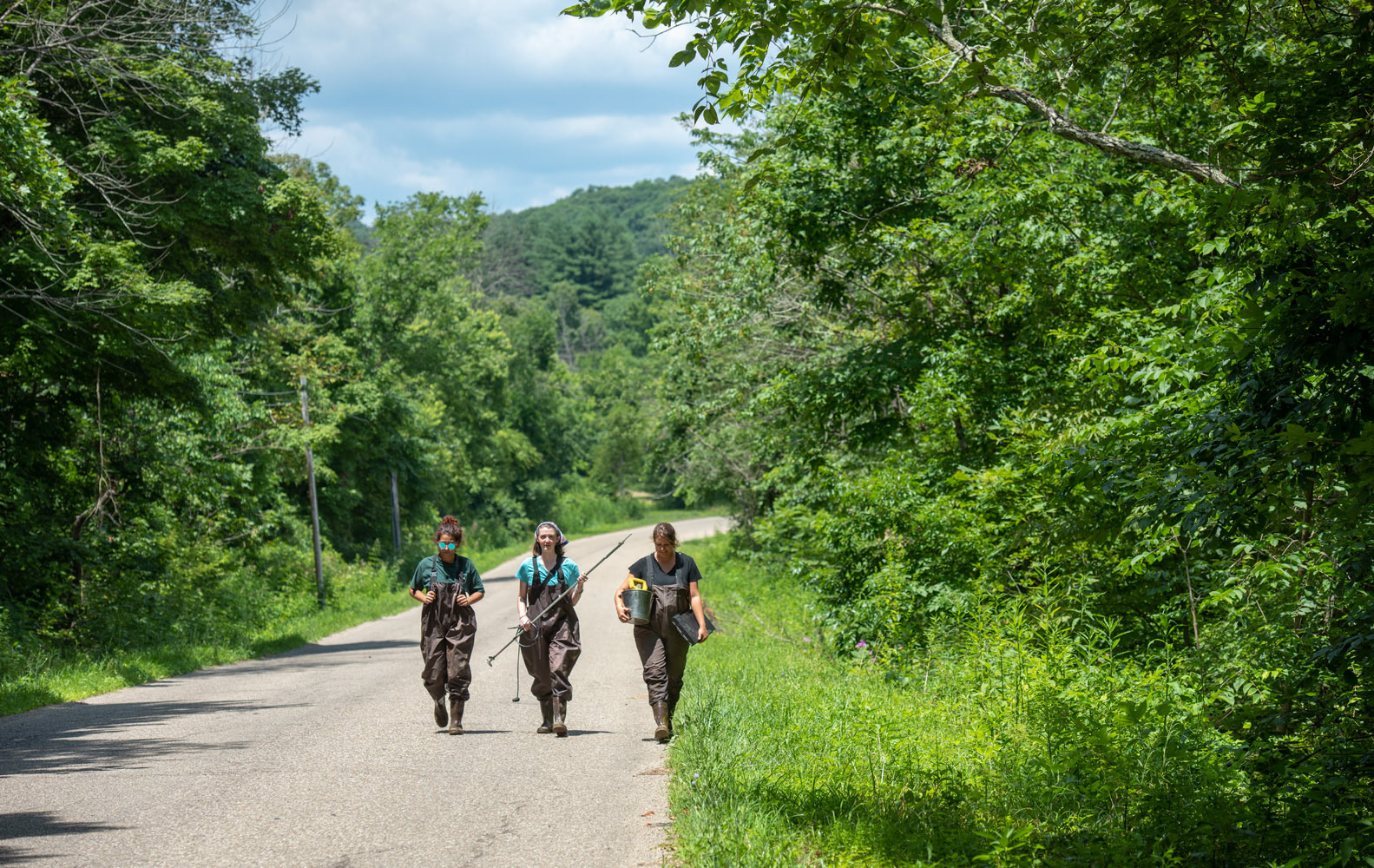
THE PILOT PLANT
Students have helped develop the design of the pilot facility, which features three tanks. Water is pumped from the creek 15 feet up to the first tower of the facility and falls through a series of three aeration trays (which are manufactured from reclaimed industrial waste). Aeration brings the water and iron in contact with oxygen, creating the necessary chemistry to start formation of iron oxide. Next, in the two settling tanks, the iron and water sit as visible crystals of rust-colored iron oxide form. Finally, the acidic water is released from the tanks through a bed of slag, a waste product of the steel industry that is alkaline in nature, to neutralize the water before it re-enters the stream. Eventually, the slag loses its alkaline properties; Sabraw explains that the team is engineering a process to remove it and replace it with fresh material every few weeks. The old slag can be used as gravel, Riefler adds.
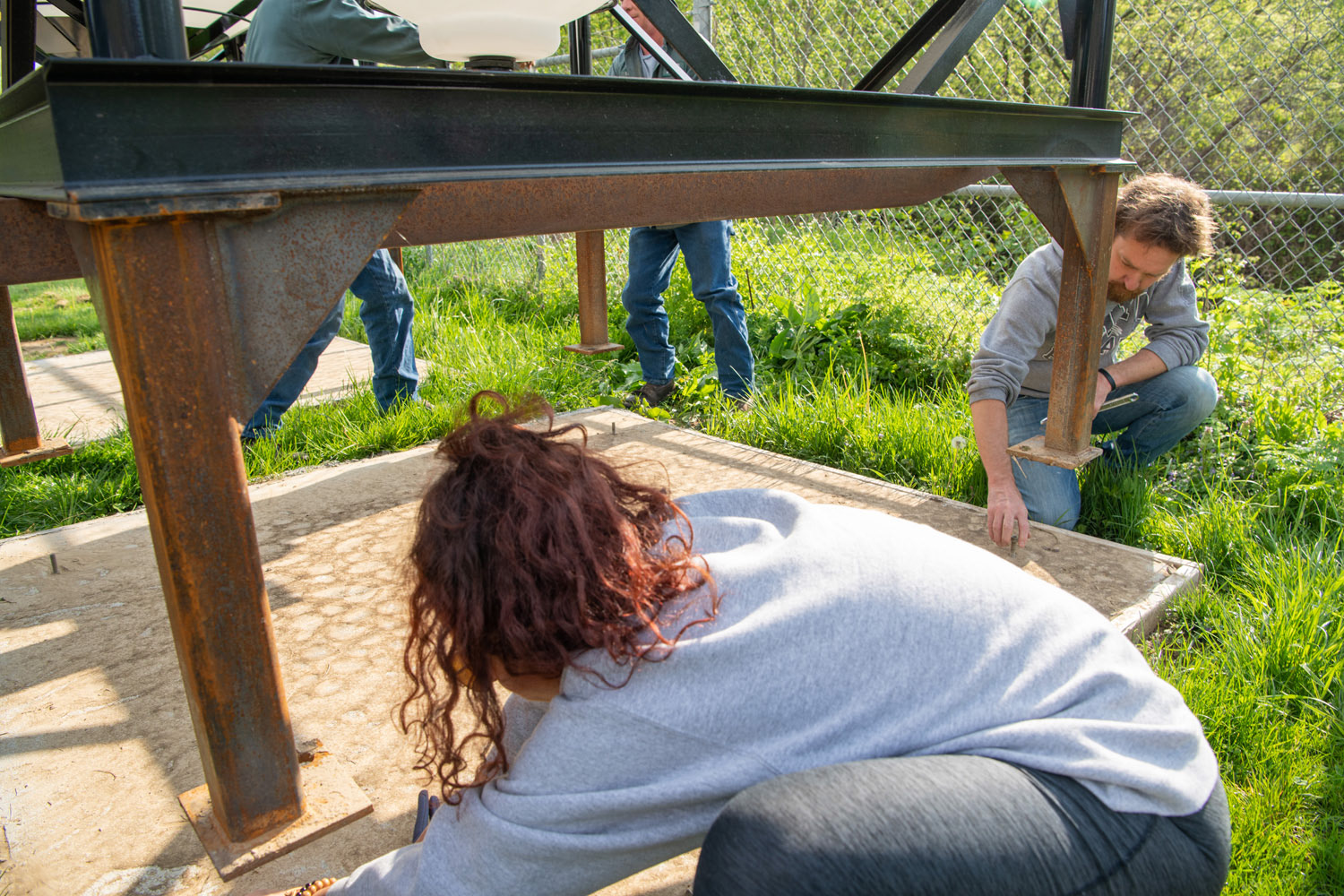
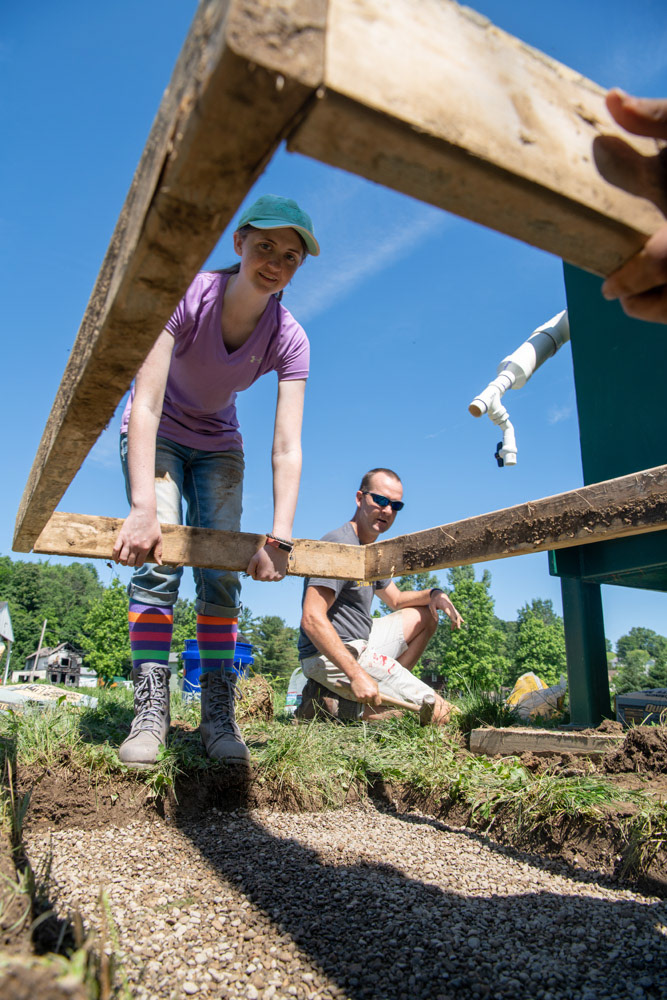
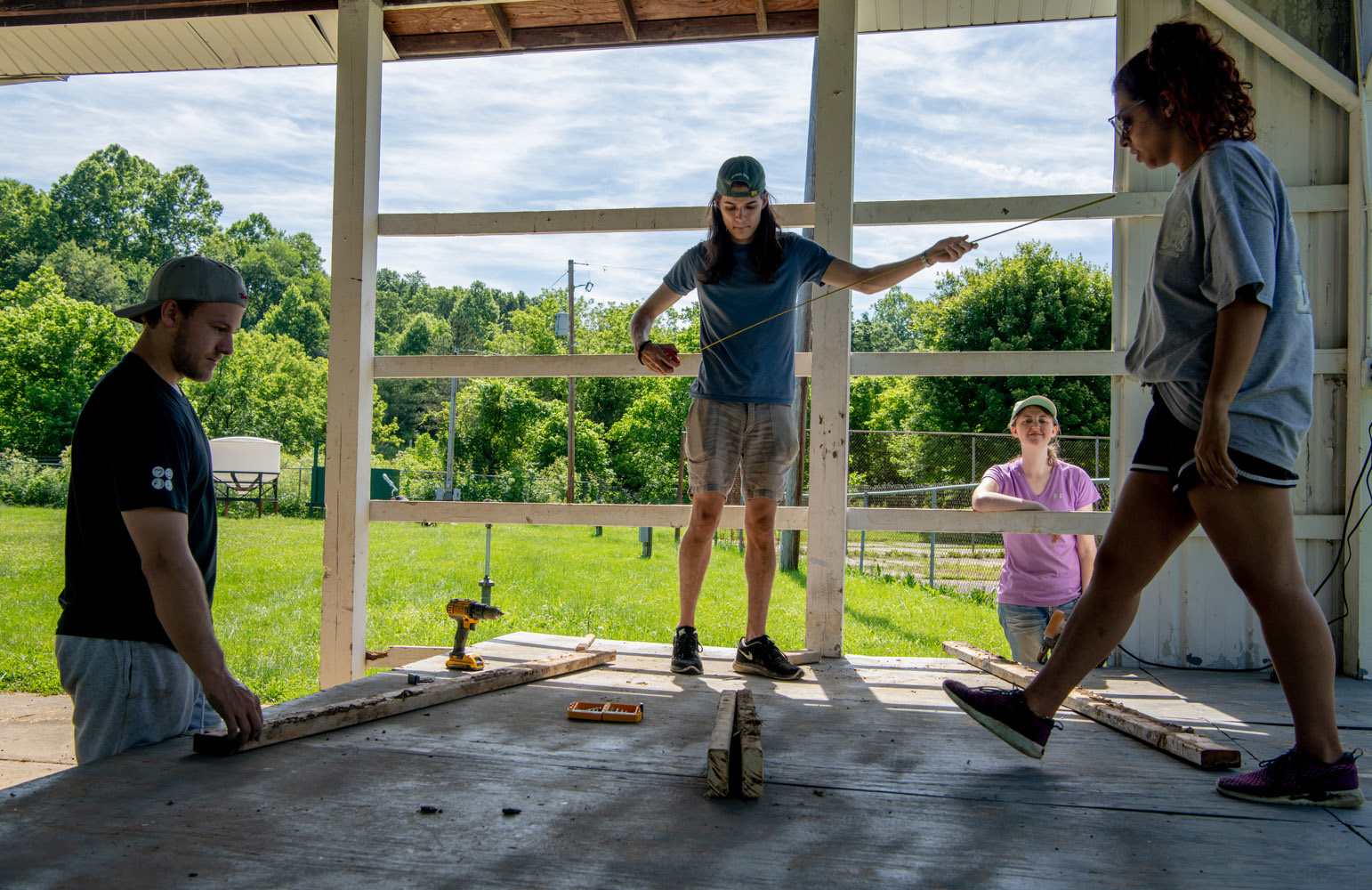
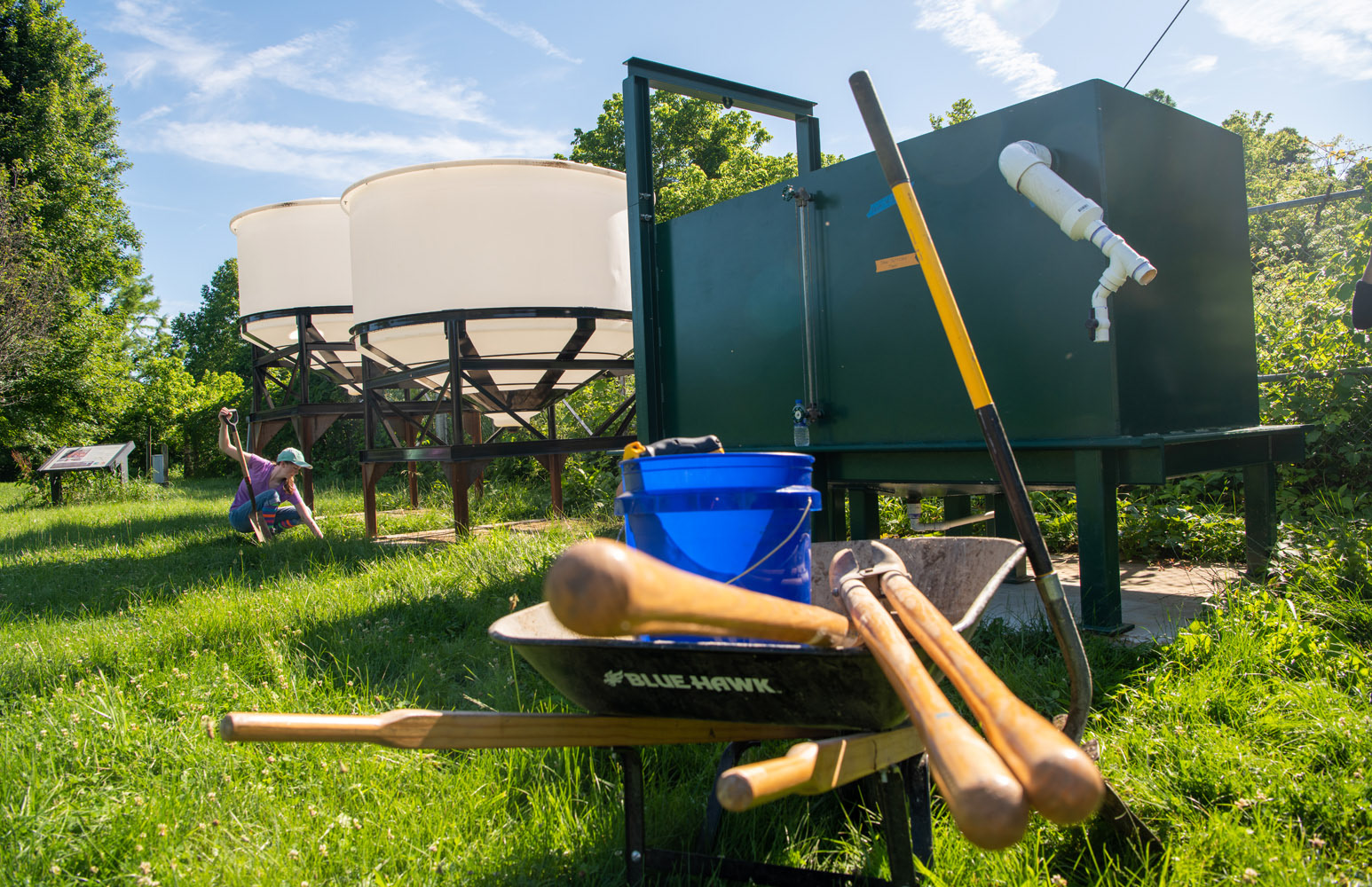